Table of Contents
What Is Drilling Mud?
Drilling mud is a crucial component used to facilitate the drilling process of boreholes into the Earth’s surface. Drilling mud also called as drilling fluid.
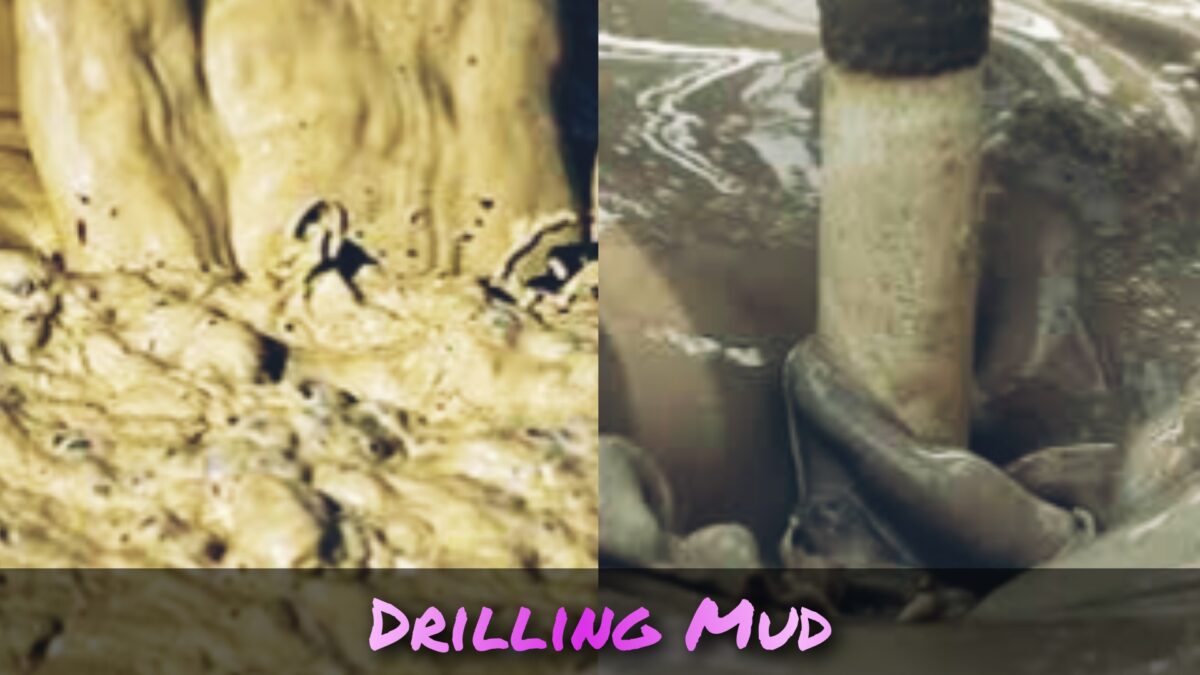
Its applications range from drilling oil and natural gas wells to simpler tasks like water well exploration. One of the primary purposes of drilling mud is to transport cuttings out of the borehole.
There are three primary categories of drilling fluids: water-based muds (WBs), which can be either dispersed or non-dispersed; non-aqueous muds, commonly referred to as oil-based muds (OBs); and gaseous drilling fluids, which encompass a wide range of gases. These drilling fluids, combined with appropriate polymer and clay additives, are employed for drilling various oil and gas formations.
The fundamental functions of drilling fluids encompass several critical aspects. They provide hydrostatic pressure, which prevents the influx of formation fluids into the wellbore. Additionally, they assist in cooling and cleaning the drill bit throughout the drilling process. Drilling fluids are responsible for conveying the drill cuttings away from the borehole and suspending them when drilling operations are paused or when the drilling assembly is being maneuvered in and out of the hole. It is imperative to select the appropriate drilling fluid for a specific job to minimize formation damage and mitigate corrosion risks.
I would also recommend you to read my article on Autonomous Directional Drilling.
Importance Of Drilling Mid In Drilling Operation
Drilling muds are important for controlling the drilling process and keeping the wellbore stable. They help to hold the cuttings in place when drilling stops and carry them to the surface when drilling resumes. These muds also clean, cool, and lubricate the drill bit. They create a protective layer on the surrounding rocks to keep them isolated. Drilling fluids can be made of water or other substances and are chosen based on the type of ground and how the well is being drilled.
Cement is used to fill the space between the casing and the wellbore. It provides support and acts as a barrier to prevent corrosion of the metal and stop oil, gas, or water from flowing through the space between the casing and the wellbore. This barrier protects sources of clean water and prevents unwanted substances from entering the well. Cement is also used when a well is no longer in use or needs maintenance.
Properties Of Drilling Mud
- Drilling mud has a controlled viscosity that helps it carry drill cuttings to the surface.
- Drilling mud is formulated with a specific density higher than the formation being drilled to control pressure and prevent well blowouts.
- Drilling mud effectively controls fluid loss into the formation by creating a filter cake on the wellbore wall.
- Drilling mud acts as a lubricant, reducing friction and heat between the drill string and wellbore walls.
- Drilling mud suspends and transports drill cuttings and solid particles to maintain a clean wellbore and protect drilling equipment.
- Drilling mud controls filtration to prevent the invasion of fine particles and contaminants from the formation.
- Drilling mud maintains pH stability to prevent corrosion of equipment and ensure optimal performance.
- Drilling mud formulations are designed to be environmentally compatible, minimizing their impact on the ecosystem and meeting regulatory requirements.
Types Of Drilling Mud
1. Water-Based Mud (WBM):
Water-based mud is a special kind of liquid made mostly of water that helps in drilling holes in the ground. It has some other things mixed in it to make it work better. People use this type of mud when they are digging not too deep.
2. Oil-Based Mud (OBM):
Oil-based mud is another kind of liquid used for drilling holes in the ground. It is made with oil and some other things that help the drilling process. This mud is used when people are digging really deep holes or in very hot places.
3. Synthetic-Based Mud (SBM):
Synthetic-based mud is a type of liquid used for drilling holes. It is made with special man-made fluids instead of natural oils. This mud is used when people need to be careful about the environment or when drilling really deep in the water.
4. Air Drilling Fluid:
Air drilling fluid is a special way of drilling that uses compressed air or a mix of air and foam. This method is used when drilling in certain types of ground where water or regular mud can cause problems. It helps drill holes quickly, but it doesn’t work in all places.
5. Foam-Based Mud:
Foam-based mud is a special kind of liquid made by mixing gas (like air) with water or oil-based mud. This mixture becomes lighter and flows better, which helps in drilling holes in certain types of ground. It is used when the ground is very easy to let the mud escape.
6. Aerated Drilling Fluid:
Aerated drilling fluid is a special way of drilling that uses air or gas mixed with water or mud. It is used in special situations like drilling for hot water underground or getting natural gas from the ground. This method is different from regular drilling.
Faqs
Drilling mud can face challenges like staying stable, not losing too much fluid, being the right thickness, avoiding contamination, and being environmentally friendly. These issues are addressed by adding the right chemicals, regularly checking the mud’s properties, using good drilling techniques, and following rules for disposing and recycling.
Thickness, or viscosity, of drilling mud is controlled by adding special substances called viscosifiers or modifiers. It’s important to control viscosity because it affects how well the mud carries away the bits of rock and keeps the hole clean. The right thickness allows for smooth drilling and better control.
There are different things added to drilling mud that serve specific purposes. Some common additives are used to make it thicker (like bentonite), prevent fluid loss (like polymers), mix the mud with water (like surfactants), control pH levels (like lime), and stabilize the rock (like potassium chloride). These additives give the mud the right properties for drilling.
The performance of drilling mud is checked by regularly testing it. They measure things like density, thickness, pH level, how well it filters, how it moves, and how much solid stuff is in it. They might also do extra tests to analyze the weight, the mud that sticks to the hole, and the chemicals in it. These tests help them keep the mud in good shape, fix any problems, and make sure drilling goes smoothly.
To stay safe when handling drilling mud, there are some important things to do. Wear protective gear, make sure the area has good airflow, avoid eating or touching the mud directly, and follow the rules for preventing and cleaning up spills. Regular training and following safety guidelines are really important to keep everyone safe and avoid risks when dealing with drilling mud.