A pneumatic actuator is a mechanical device that converts energy into mechanical movement, usually compressed air. These actuators have different names such as Air actuators, air cylinders, and pneumatic actuators. All types of pneumatic actuators have the same working principle.
Actuators consist of ports, valves, cylinders, or pistons that can convert energy into rotational or linear mechanical motion. This depends on whether the application uses a pneumatic linear actuator or a rotary actuator.
The linear actuator works well with angle seat control valves for high steam, high-temperature applications. In contrast, rotary pneumatic actuators work well with rotary valves, depending on the specifications of the application.
The Pneumatic Actuator has high reliability, efficiency, and safety source for motion control. These are ideal for repeatedly opening and closing valves and other industrial functions where electricity can pose a fire. In the chemical and manufacturing industries, actuators are commonly used to control valves that control the movement of fluids.
The figure below shows a simplified image of a pneumatic actuator. It works with the combined effect of spring force and air. The actuator adjusts the position of the shut-off valve by transmitting the movement of the shut-off valve to the valve stem.
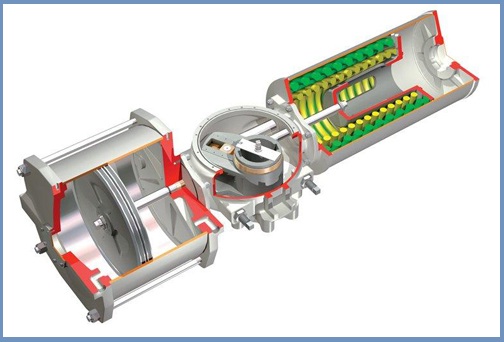
The rubber membrane divides the drive housing into two air chambers. The upper chamber is ventilated through the opening at the top of the housing. The lower chamber has a spring that pushes the membrane, as opposed to the mechanical stop of the upper chamber. Finally, a local gauge is connected to the valve stem to indicate the position of the valve. The position of the valve is controlled by changing the intake air pressure in the upper chamber. This process changes the force exerted on the top of the membrane.
Table of Contents
How Does a Pneumatic Actuator Work?
The process of how a pneumatic actuator works are known as the operating principle of a pneumatic actuator. There are two types of pneumatic actuators: diaphragm and piston actuation.
Pneumatic actuators efficiently use compressed air to generate drive energy. The air in the instrument stores the force or pressure acting on the diaphragm or piston. This moves the valve actuator into place on the valve stem, resulting in mechanical movement.
The use of air to power this movement can be summarized in two factors. It is easy to compress and absorb and is safer than other gases. Because of this, and because the conversion of compressed air to kinetic energy can be controlled very well, pneumatic actuators are a very popular device in the industrial manufacturing industry.
Various Types of Pneumatic Actuators
- Rotary Actuators
- Tie Rod Cylinders
- Grippers
- Rodless Actuators
- Vacuum Generators
Advantages
- It gives high power and speed of movement.
- It is very durable and long-lasting.
- pneumatic actuators are very reliable in their operation.
- Clean technology.
- Cost is low.
Disadvantages
- Due to the compressibility and pressure loss of the air, compressed air systems are less efficient than other techniques.
- Limited compressor and air supply mean running at lower pressure will result in slower speeds and less power consumption.
- To be truly effective, pneumatic actuators must be sized for a particular task.
- This requires relatively sized compressors, regulators, and valves, which increases complexity and cost. Therefore, it cannot be used in any other application.
- While air can easily penetrate, it can mix with lubricants or oils, leading to downtime and maintenance.
- Industries still have to pay for compressed air, making it usable, and maintenance costs for compressors and piping.
- It has low control accuracy.
- He has the best performance at a slow speed.