Table of Contents
Introduction
Hydrogen induced cracking (HIC) is a type of wet H2S cracking and is typically produced by high concentrations of hydrogen in metals. This mechanism involves the diffusion of atomic hydrogen into the metallic structure. Cracks caused by HIC are formed parallel to the plane and in the hoop stress direction.
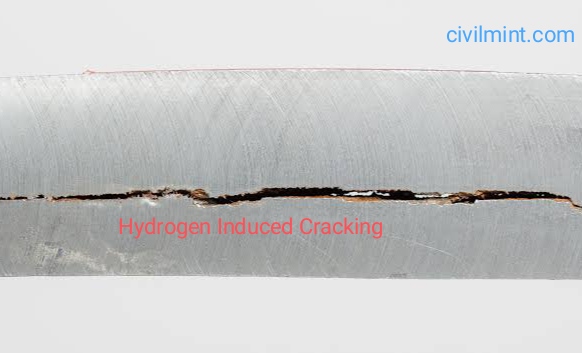
Hydrogen cracking is more common in acidic operating environments because wet he H2S is present. There are several other factors that contribute to hydrogen-induced cracking. These elements include arsenic, antimony, selenium, and cyanide. However, H2S is believed to be the most important cause of hydrogen-induced crack damage in the oil and gas industry. HIC causes blistering damage to many metals and alloys.
Hydrogen induced cracking is more common in ferrous alloys due to the limited lubricity of the BCC structure. HIC generally damages steels with a Rockwell C hardness of 22 or higher at relatively low temperatures.
HIC can also occur in a variety of high temperature processes such as electroplating, pickling, phosphating, cathodic protection, and arc welding.
How Does it Occur?
This mechanism begins with the formation of atomic hydrogen, which diffuses within the metal or alloy and accumulates in voids or impurities within the metallic structure.
When these hydrogen atoms combine to form hydrogen molecules, a high pressure is created inside the cavity. H2S pushes these hydrogen atoms into the metal structure, reducing the ductility and tensile strength of the metal.
This mechanism slowly reduces the ductility of the metal and gradually forms internal cracks known as hydrogen-induced cracking.
Preventive Measures
Hydrogen embrittlement can be prevented in several ways, all aimed at minimizing metal-hydrogen contact, especially during water generation and electrolysis. Brittle processes such as pickling should be avoided as they increase contact with elements such as sulfur and phosphates. Using proper electroplating solutions and processes also helps prevent hydrogen embrittlement.
If the metal has not yet begun to crack, hydrogen embrittlement can be reversed by removing the hydrogen source and allowing the hydrogen to diffuse into the metal through heat treatment. This debrittlement process, known as low-hydrogen annealing or “baking,” is used to overcome the weaknesses of processes such as electroplating that introduce hydrogen into metals, but must be achieved for sufficient time and time. is not always completely effective. temperature. A test such as ASTM F1624 can be used to quickly determine the minimum bake time (tests using Design of Experiments allow this value to be accurately determined using a relatively small number of samples). The same test can then be used as a quality control check to assess whether baking was successful on a batch basis.
During welding, metals are often preheated and reheated to allow hydrogen to diffuse before causing damage. This occurs especially in high-strength steels and low-alloy steels such as chromium/molybdenum/vanadium alloys. Hydrogen cracking due to welding can occur more than 24 hours after the welding process is complete, as hydrogen atoms take time to recombine into hydrogen molecules.
Another way to prevent this problem is material selection. This builds an inherent resilience against this process and reduces the need for post-processing and constant monitoring for errors. Certain metals or alloys are very prone to this problem, so the best solution is to choose a material that minimizes degradation while maintaining the desired properties. Much work has been done to catalog the compatibility of specific metals with hydrogen. Using tests such as ASTM F1624 to rank alloys and coatings in material selection can also do. For example, you can check that the crack threshold is below the threshold for hydrogen stress corrosion cracking. Similar tests can also be used during quality control to more effectively qualify materials produced in a rapid and comparable manner.