Table of Contents
Introduction of Hydrophobic Cement?
Hydrophobic Cement is used in highly wet climatic conditions. The other names of Hydrophobic Cement are Hydrographic cement and Repellant Cement.
Hydrophobic cement is a type of cement containing additives that reduce the wettability of cement particles by forming a thin water-repellent film around the cement particles. This film tears when water is added to the cement and does not interfere with the cement’s normal hydration in any way.
Common hydrophobic additives include acidol, naphthenic soaps and petrolatum oxide.
What is Super Hydrophobic Cement?
Super Hydrophobic Cement also called as luminescent cement. It is known as luminescent cement because it reflect light.
This types of cement is made by modifying the cement structure. Because it absorbs and reflects light, it is an eco-friendly material and a substitute for street lighting.
Super Hydrophobic Cement can be a great solution for lighting streets and buildings without electrical installations. Such cement is claimed to be able to glow for up to 12 hours when exposed to sunlight for the same amount of time.
Chemical Composition of Hydrophobic Cement
A little quantity of hydrophobic admixtures are mixed into the OPC clinker during grinding. These hydrophobic admixtures such as oleic acid, boric acid and stearic acid are added to clinker at a rate of 0.1 to 0.5% by weight of cement as a dry additive.
Manufacturing Process
Manufacturing process of hydrophobic cement is very simple. Hydrophobic cement is made by grinding grade 33 OPC clinker well mixed with natural or chemical gypsum and 0.1-0.5% by weight of clinker of a hydrophobic agent.
How it Works
If you want to use hydrophobic cement then it is very important to know how it work.
I have described the working process of hydrophobic cement.
Hydrophobic cement is made by grinding regular Portland cement clinker mixed with hydrophobic film formers such as oleic acid, boric acid and stearic acid. A thin hydrophobic film forms around each particle of cement, slowing down the rate of cement degradation.
Cement readily decomposes during long-term storage, transportation, or under unfavorable conditions.
The thin film around the cement particles prevents the penetration of atmospheric moisture and prevents the cement from deteriorating due to the above reasons.
In hydrophobic cement, when cement and aggregate are mixed with water to form concrete, the hydrophobic film around the cement particles breaks down, exposing the cement particles to normal hydration processes.
Chemical Properties of Hydrophobic Cement
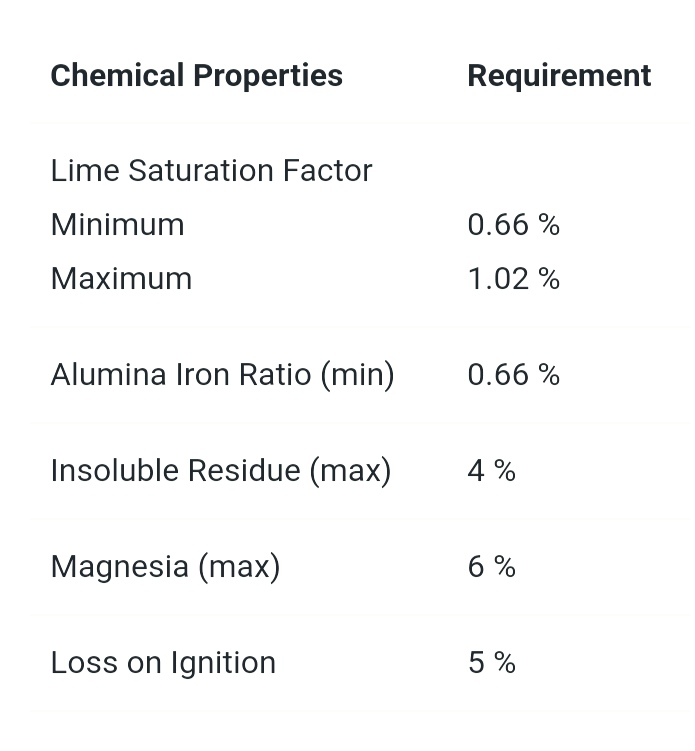
Physical Properties of Hydrophobic Cement
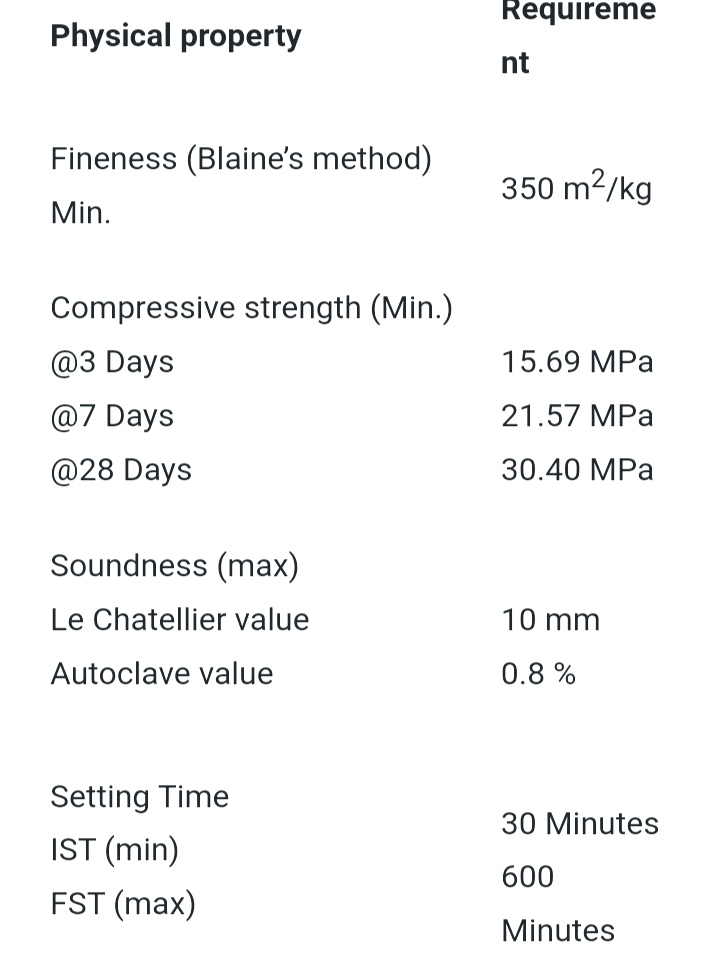
Applications and Uses of Hydrophobic Cement
- For long-term storage and extremely humid climatic conditions.
- Mainly used in tunneling, as underground repairs are difficult and expensive.
- These cements are used in the construction of dams, spillways and underwater structures.
- Used on structures exposed to rain and puddles. B. Green roofs, other types of roofs, parking lots, open spaces.
- Used for drainage systems and manholes.
- Used for water treatment plants, dams and retaining walls.
- Repair leaky pipes and basements without stopping the leak.
Pros
- Strength is equivalent to ordinary cement.
- Usually cures in 3 minutes after mixing with water.
- Fast curing time, fast curing, can be painted within 1 hour after application.
Cons
- Does not work on frozen surfaces.
- Cannot be used in temperatures below 40 degrees Fahrenheit.
- This cement solves the leak problem, but not the problem caused by condensation.
- The use of this type of cement requires skilled labor and favorable climatic conditions.
- High cost because it is very expensive.