This article explains about oil well cement, oil well cementing, and cement casing oil well. We will explore all the important things related to oil well cement.
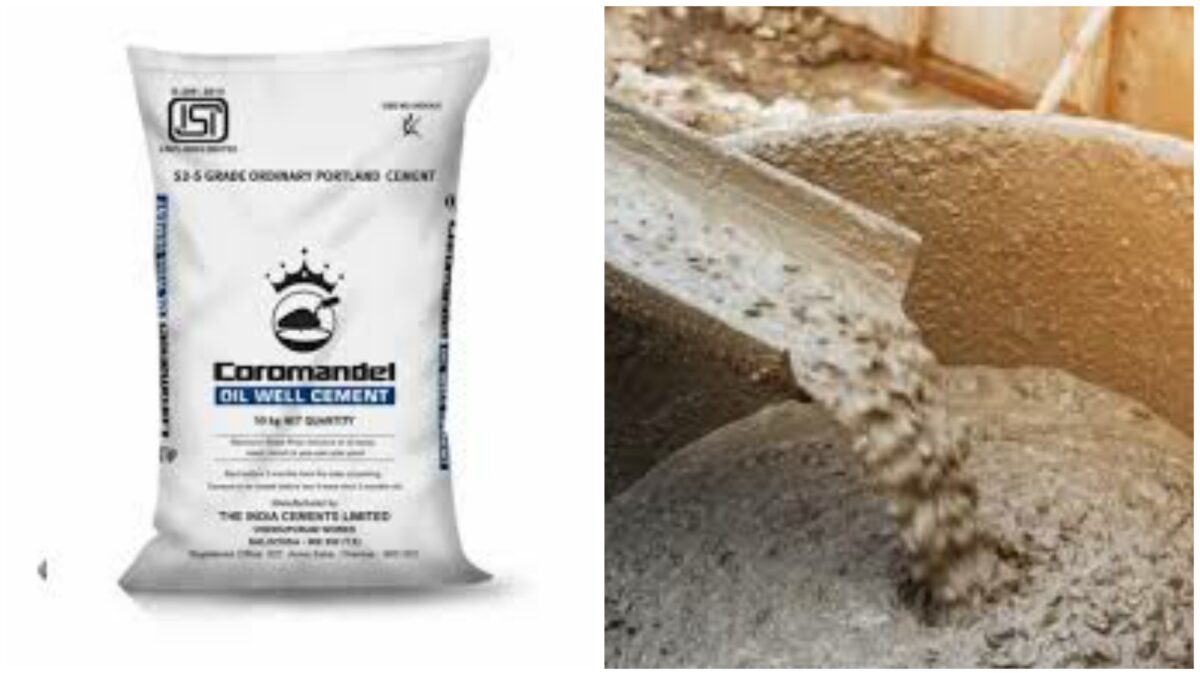
Table of Contents
What Is Oil Well Cement?
The oil well cement is used for the purpose of securing oil-well pipe casing with the surrounding
earth and rocks.
This type of cement is manufactured by grinding clinker consisting essentially of hydraulic calcium silicates. No material other than calcium sulphate be interground or blended during manufacture of cement.
But, set modifying agents like lentonite, barite and fly ash may be added in classes D, E and F types of oil well cement.
The oil-well cement are classified as A, B, C, D, E, F, G, H and J-class based upon its use at particular depth from ground level and the surface condition.
Classification Of Oil Well Cement
- Class A – Suitable for use up to a depth of 1830 m, without any special requirements.
- Class B – Suitable for use up to a depth of 1830 m, when conditions require a moderate to high degree of sulphate resistance.
- Class C – Suitable for use up to a depth of 1830 m, when conditions require an ordinary to high degree of sulphate resistance and high early strength.
- Class D – Suitable for use at depths between 1830 and 3050 m, when conditions require a moderate to high degree of sulphate resistance under moderately high temperatures and pressures.
- Class E – Suitable for use at depths between 3050 and 4270 m, when conditions require a moderate to high degree of sulphate resistance under high temperatures and pressures.
- Class F – Suitable for use at depths between 3050 and 4880 m, when conditions require a moderate to high degree of sulphate resistance under extremely high temperatures and pressures.
- Class G – Suitable as a basic cement for use up to a depth of 2440 m, when conditions require a moderate to high degree of sulphate resistance, and can be used with accelerators and retarders to cover a wide range of well depths and temperatures. No additions other than calcium sulphate or water, or both, shall be interground or blended with the clinker during manufacture.
- Class H – Suitable as a basic cement for use up to a depth of 2440 m, when conditions require a moderate degree of sulphate resistance, and can be used with accelerators and retarders to cover a wide range of well depths and temperatures. No additions other than calcium sulphate or water, or both, shall be interground or blended with the clinker during manufacture.
- Class J – Suitable for use at depths between 3660 and 4880 m, when conditions require a moderate to high degree of sulphate resistance under extremely high temperatures and pressures, and can be used with accelerators and retarders to cover a wide range of well depths and temperatures. No additions other than calcium sulphate or water, or both, shall be interground or blended with clinker during manufacture.
Oil Well Cementing
Oil well cementing is a difficult task in oil and gas industry. In this process, cement is placed into the annular space between the wellbore and the casing to create a solid and impermeable shield.
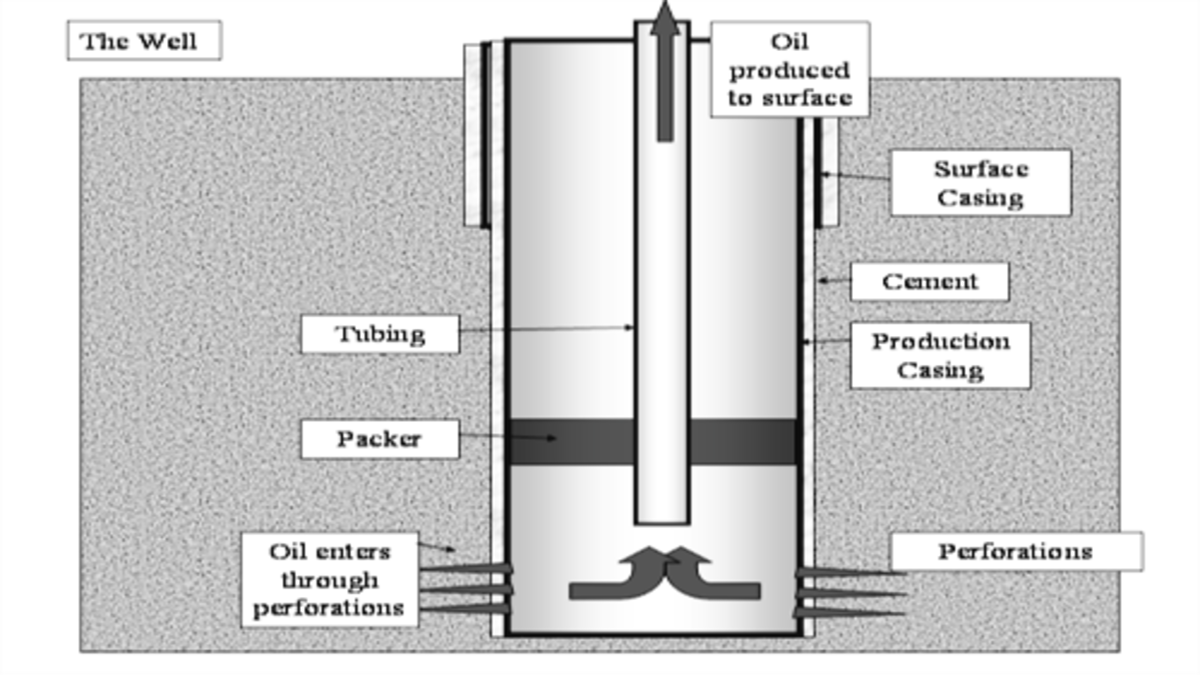
Oil well cementing is a critical process that involves the placement of cement into the annular space between the wellbore and the casing to create a solid and impermeable barrier.
Oil well cementing process is carried out in various steps as described below:
- Well preparation: Before the cementing process begins, the wellbore must be properly prepared. This includes cleaning the wellbore, checking the integrity of the casing, and ensuring that there are no obstructions or formations that may interfere with the cementing process.
- Mixing the cement: The cement used in oil well cementing is a special blend of cement, additives, and water. The mixture is prepared according to a specific recipe, which is tailored to the conditions of the wellbore.
- Pumping the cement: Once the cement is mixed, it is pumped into the wellbore through the casing. The cement is pumped at high pressure to ensure that it reaches all the way to the bottom of the wellbore and flows back up the annular space between the casing and the wellbore.
- Placing the cement: As the cement is pumped into the wellbore, it displaces the drilling mud and fills the annular space. The cement is designed to harden quickly, which helps to create a strong, impermeable barrier.
- Curing the cement: After the cement has been placed, it must be allowed to cure. The curing process can take several hours to several days, depending on the type of cement used and the conditions of the wellbore.
- Testing the cement: Once the cement has cured, it must be tested to ensure that it has created a strong and impermeable barrier. This is typically done by running a cement bond log, which uses acoustic energy to measure the integrity of the cement bond.
Oil well cementing is a challenging task and must be undertaken with care. All safety checks should be carried out before starting any operation. Workers should be aware of all safety hazards related to the work.
Cement Casing of An Oil Well
Cement casing is an important component of an oil well. It involves placing a casing made of steel or other material into the well and then filling the space between the casing and the wellbore with cement. Cement acts as a barrier that prevents oil, gas, and other liquids from escaping from the well and contaminating the surrounding rock formations or aquifers.
The process of installing the casing in an oil well involves several steps. First, the casing is lowered into the wellbore and set to the required depth. Next, a cement slurry is pumped into the space between the casing and the wellbore. Cement mortar is usually composed of cement, water, and various additives that improve its properties such as time setting, strength, and durability.
Once the cement is in place, it must be allowed to cure or harden. This process can take several hours to several days depending on the type of cement used and the conditions of the well. After the cement has cured, the casing is firmly held in place and the well can be drilled further.
Cement casing is an essential component in oil well construction and is critical to ensuring safe and efficient oil and gas production. It helps prevent well blowouts, casing failures, and other accidents that can be costly and dangerous.
Faq
Oil well cement is used to create a barrier between different geological formations to prevent the flow of fluids or gases between them in oil and gas wells. This ensures the produced fluids do not mix with other formations, which could cause contamination or reduce well efficiency.
The raw materials for oil well cement are limestone, clay, shale, and sand. These materials are ground into a fine powder and mixed with water to form a slurry, which is then pumped into the surrounding formation. Other additives may also be added to improve the properties of the cement.
The physical properties of oil well cement include compressive strength, setting time, thickening time, and density. Compressive strength is the cement’s ability to resist crushing forces, while setting time is the time it takes to harden. Thickening time refers to the time it takes for the cement to reach a certain viscosity, and density is the mass per unit volume of the cement.