Pouring concrete in cold weather is a challenging task and must be done with care. In this article I will give all the important information related to pouring concrete in cold weather.
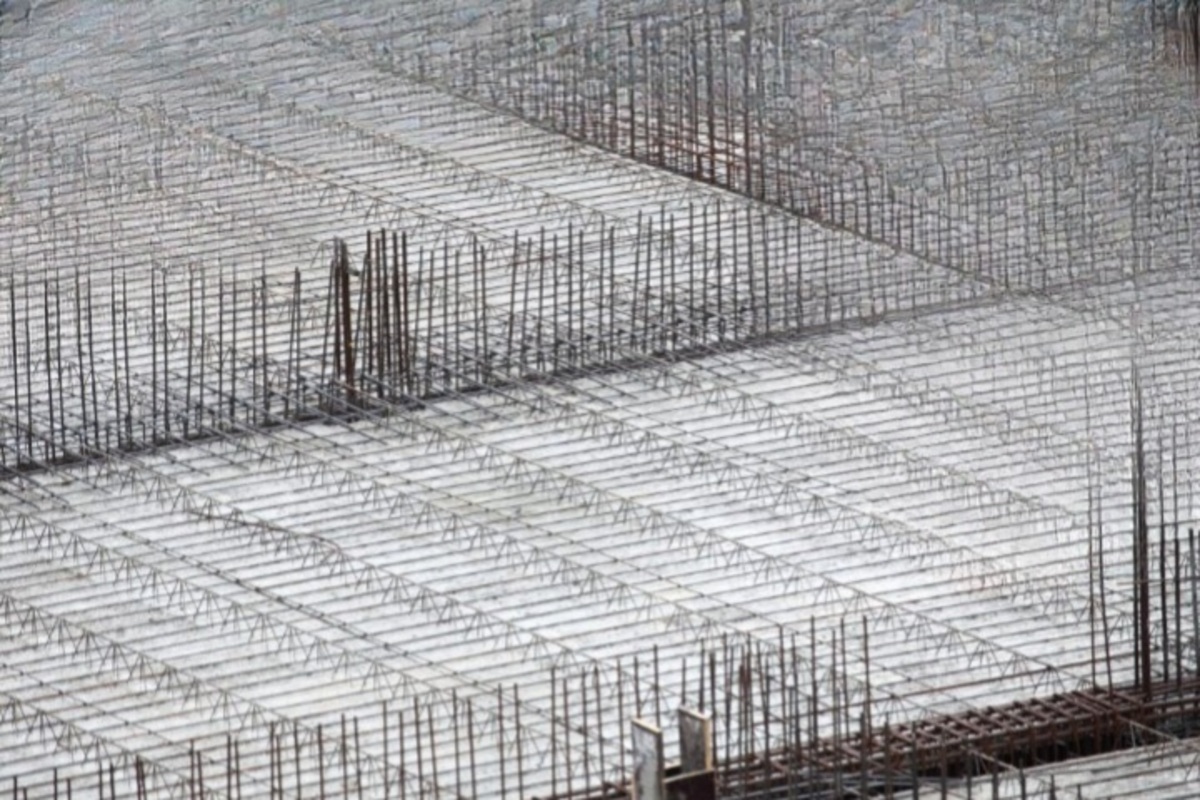
Table of Contents
What Is Cold Weather Concreting?
Cold weather concreting involves placing, finishing and curing concrete when the atmospheric temperature is 5 °C.
It requires special precautions and techniques to ensure proper curing and the desired strength and durability. Achieving these objectives can be challenging because of the low temperatures, which slow down the chemical reactions responsible for hardening and increasing the strength of concrete.
To overcome these challenges, cold weather concreting employs various methods, such as preheating the material, using cure accelerators, and monitoring temperature and humidity during the curing process. These methods are important to prevent defects such as cracking and to ensure that the concrete attains its desired strength and durability.
How Cold Weather Affects Concrete?
The process of cement hydration gives concrete its strength, and this process is affected by temperature. High temperatures speed up hydration, while low temperatures slow it down.
Research shows that cement can still undergo hydration even at temperatures as low as -10 degrees Celsius.
When water in fresh concrete freezes, it causes the concrete to expand, similar to saturated soil that heaves. The absence of available water due to freezing delays the setting and hardening of fresh concrete.
To ensure that the concrete sets without any loss of strength, it must be revibrated after thawing. If not, the concrete will set with large pores, significantly reducing its strength.
While revibrating the concrete can produce sound concrete, it is only recommended when necessary.
If the concrete has set but has not developed sufficient strength and freezing occurs, the expanding water can cause cracking, reducing the concrete’s strength.
However, if the concrete has already developed enough strength, it can resist freezing temperatures without damage. Most of the water would have combined with cement or located in small pores, making it unlikely to freeze.
Which Cement Is Used For Pouring Concrete In Cold Weather?
Using a cement that is specifically designed for use in low-temperature environments is crucial when working in cold weather conditions. One example of such a cement is Type III cement, also known as high-early-strength cement. Manufacturers produce this type of cement by grinding portland cement clinker with a higher percentage of tricalcium silicate (C3S) than regular portland cement. The increased percentage of C3S allows for faster hydration, resulting in quicker strength gain, and making it appropriate for pouring concrete in temperatures as low as 5°C (41°F).
In addition to selecting the appropriate cement, it is preferable to use cement with a higher rate of heat of hydration in cold weather conditions. Cement with rapid hardening properties or high C3S and C3A contents, along with a low water-cement ratio, is advantageous for placing concrete in cold weather. The reason for this is that a high rate of heat of hydration generates more heat during the curing process, which can prevent the concrete from cooling too fast and reaching its required strength.
However, it is critical to keep in mind that one must use proper curing techniques, as well as insulation and heating techniques, to safeguard the concrete from freezing and ensure that it reaches its maximum strength potential.
Concrete Additives For Cold Weather
Low temperatures can affect concrete in cold weather, which may result in slower setting times, lower early strength development, and an increased risk of cracking. To address these issues, concrete mixes for cold weather conditions can incorporate several additives. For instance, chemicals such as calcium chloride, sodium nitrate, and triethanolamine can be included in the mix to accelerate the setting time and early strength development, which are known as accelerators.
Air-entraining agents are chemicals that can be added to the concrete mix to create microscopic air bubbles throughout the mix, improving its workability and reducing the risk of cracking due to freeze-thaw cycles. Another type of chemical additive is the retarders, which slow down the setting time and are useful in cold weather conditions where the concrete may set too quickly, leading to reduced strength development and poor quality. Common retarders include sugar, lignosulfonates, and citric acid.
To improve the concrete’s resistance to cracking, synthetic macro fibers can be added to the mix, reinforcing it and preventing cracks from forming due to thermal cycling. It is worth noting that the specific project and weather conditions determine the type and amount of additive needed. Therefore, it is advisable to consult with a concrete expert or supplier to determine the most appropriate additive for your project.
Faqs
Yes, but it requires special precautions.
Around 40°F (4.4°C), but it depends on the project.
Use a low water-to-cement ratio mix, add accelerators, insulate the concrete and monitor the temperature.
Reference: ACI 306R-16 “Guide to Cold Weather Concreting