Table of Contents
Introduction of Pumped Concrete
Pumped concrete is concrete that is pumped and transported by using special types of pumps. Mixed concrete can be transported easily from one place to another. This method is used when large amounts of concrete work are required at heights that are not easily achievable by other means of transport.
Large quantities of concrete can be pumped over considerable distances through pipelines, often to locations not easily accessible by other means of transportation.
Concrete is mixed in batching plant. It is consist of Hooper. Concrete is send to Hooper from the concrete mixer. Mixed concrete finally delivered via pipeline.
Types of Concrete Pump
I have described various types of concrete pumps. These pumps normally used to pump concrete.
1. Direct Acting Concrete Pump
The majority of concrete pumps are direct acting horizontal piston pumps with swivel valves. Direct-acting pumps are easy to operate.
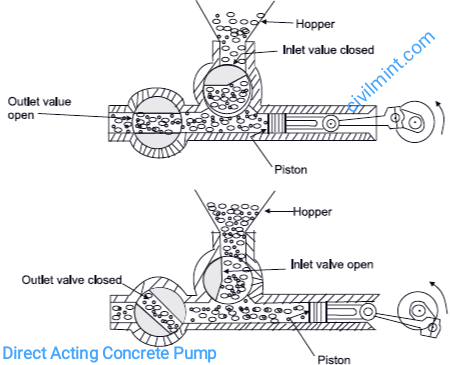
Concrete is fed to the pump by gravity and in part by suction caused by the reciprocating motion of the horizontally acting pistons as the swing valve alternately opens and closes. Under good conditions, a suction pressure of approx. 0.08 N/mm² is generated in the pump cylinder. When the diameter of the suction pipe matches the diameter of the pump cylinder, optimum suction conditions are achieved and concrete can flow unhindered. Concrete must be able to flow freely across the cross-section of the suction pipe, avoiding the possibility of blockage by too large aggregates.
Ideally, the diameter of the suction tube should be at least three times the maximum aggregate size of the concrete to be pumped. Therefore, the draft tube diameter determines the maximum aggregate size that can be used for the particular concrete mix being pumped.
During the “suction stroke”, the inlet valve opens, concrete flows into the pump cylinder, and the outlet valve remains closed. In the “delivery stroke”, the outlet valve is opened and the inlet valve is closed, pushing the concrete into the delivery line.
Concrete moves in a series of impulses, keeping the conveying pipes full at all times. A delivery line with a diameter of 220 mm can achieve capacities of up to 60 m3/h with modern pumps.
2. Squeeze Type Concrete Pump
A squeeze pump is a small, portable peristaltic pump. Concrete from the hopper is conveyed by rotating paddles on a flexible pipe connected to a pump chamber under vacuum of approximately 0.08 N/mm2.

The vacuum ensures that the shape of the pipe remains cylindrical, except when compacted by the rotating rollers, allowing continuous flow of concrete.
Two rotating rollers mounted on planetary gears gradually squeeze the flexible pipe, pushing the concrete into the delivery pipe. Squeeze pumps can be used to achieve capacities of up to 20 m3/h on pipelines with a diameter of 75 mm.
3. Truck Mounted Concrete Pump
Due to their large size, these types of concrete pumps are ideal for long highway and highway projects. These types of pumps are mounted on trucks and use a remotely controlled articulated robotic arm, commonly called a “boom,” to precisely spread concrete around a job site. Automatic mast pumps are another name for them. These pumps also include hydraulic arms that can manipulate pipelines containing concrete, allowing them to reach along, up and down pipelines, and even around tight spots and obstacles.

These types of concrete pumps are highly recommended for concrete projects where site space is limited or there are many obstacles in the way the concrete needs to be moved. And the multi-purpose robotic arm saves a lot of effort.
4. Fixed Concrete Pump
Fixed pumps are less manoeuvrable. Concrete pumps are mounted on a trailer or attached to a vehicle and contain flexible rubber or steel hoses that are connected to the outlet of the machine. These hoses can be connected to other extension hoses to reach anywhere concrete needs to be stored, but are less maneuverable than boom pumps. Trailer pumps pump concrete more slowly than boom pumps and are used in applications that require a small amount of pumping.
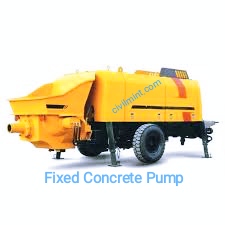
5. Special Purpose Pump
One of the most readily available types of concrete pumps is the special purpose pump. Special purpose pumps can be specially designed for use in certain types of construction projects such as Mining or tunnel construction. These pumps are expensive and work through a different mechanism, so they are rarely used. They are mounted on the frame or mounted on rails.
How to Choose Concrete Pump?
A concrete pump is selected based on two main parameters: the maximum desired volumetric flow rate of concrete per hour and the peak pump pressure p. A rated capacity of 30 m3/h is considered sufficient for regular pouring in most civil engineering applications.
Pumps with capacities in excess of 120m3/h are known to be used for special jobs requiring higher performance. The performance required for the driving device of a concrete pump varies depending on the desired concrete discharge amount Q and discharge pressure p.
Discharge rate and discharge pressure are related by the formula for the hydraulic discharge rate H of a concrete pump.
H = Q×P = Constant
Sum Up
The main problems encountered when pumping concrete are pipe blockages, as well as separation and bleeding of the concrete mix. Blockage is the inability of concrete to rise up at the end of a pipe. It is characterized by an observable increase in pressure on the manometer.
I hope you got some idea about pumped concrete. Thanks for reading my blog post.
Keep Learning!
Ta!Da!😊