In this article I will explain why crushed stones are used in railway track. I will also describe related info regarding ballast used in railway track.
Before taking deep dive into the article, let’s get brief idea of crushed stone.
Table of Contents
Crushed Stone In Railway Track
The technical word for these crushed stones is “Ballast or track ballast. The tamping machine is used to pack the track ballast under railway tracks to make the tracks long-lasting. Normally, a 25–30 cm thick ballast layer (crushed stone 30/60) below the bottom face of the sleeper is provided along the track. This thickness varies depending on many parameters and conditions.
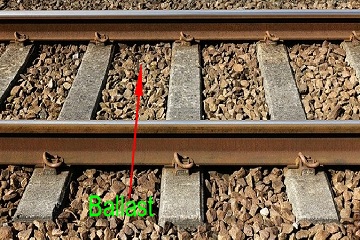
Why Crushed Stones are Used In Railway Track?
Following are the reasons for using crushed stones on railway track:
- To hold the sleepers in place, both laterally and longitudinally (as they, in turn, hold the rails in place & aid maintain gauge.
- To dispense a load of whole moving cargo from rails into the sub-base/formation (ground below the ballast).
- To keep the support of and distance between the cross ties.
- To restrain heat expansion & contraction (due to thermal stresses), and ground motion.
- To dampen the vibrations — as ballast provides a cushioning effect (hence rendering elastic property to the railway track).
- To absorb vibrations — The air voids present between the stones absorb vibrations and make it cozy, not only for the traveling passengers but also for the residents next to tracks.
- To provide drainage & stop building up of precipitation from rough weather (which can help — relieve frost heaves & maintain necessary shear stress in sub-base).
- To defeat weed & plant growth from underneath.
- To acquire much of the sounds & noises produced by train movements.
- Minor adjustments can be made in the track as and when needed.
Why Ballast Is Used In Railway Track?
Railway tracks require ballast to provide stability and support for the rails, sleepers, and other track components. Ballast is a layer of coarse materials, such as crushed stones or gravel, that is placed beneath the sleepers and around the rails. This layer of ballast helps to distribute the weight of the train and allows water to drain away from the tracks.
Ballast is important in railway tracks for several reasons. It provides stability to the tracks by distributing the weight of the train over a wider area. This reduces the pressure on the tracks and prevents them from sinking into the ground, which is essential for safe and smooth train operation.
Ballast helps to prevent waterlogging and reduces the risk of track erosion and damage by allowing water to drain away from the tracks. This is important because standing water can cause the tracks to become unstable and lead to derailments or other accidents.
Ballast acts as a shock absorber, which reduces the impact of vibrations caused by passing trains. This helps to prevent damage to the tracks and makes for a more comfortable ride for passengers.
Which Stone Used In Railway Track?
Several components make up railway tracks, including rails, sleepers or ties, and ballast. Engineers lay ballast, which is a layer of coarse stone or gravel, on the ground and beneath the railway sleepers to provide stability and support for the tracks.
The purpose of ballast is to distribute the load of the rails and trains over a larger area and provide drainage while preventing vegetation growth. The weight of trains would cause the sleepers to sink into the ground without ballast, which could lead to instability, derailment, and damage to the tracks.
Engineers choose stones for ballast based on factors such as availability, cost, and durability. Granite, trap rock, limestone, and gravel are common types of stones used for ballast. Granite and trap rock are the most frequently used because they are hard, durable, and resistant to weathering and erosion. Limestone is also popular because it is inexpensive and readily available in many areas.
To lay the ballast, workers evenly spread it over the prepared ground and level it to a uniform depth using specialized equipment such as ballast tampers and compactors. The depth of ballast used depends on factors such as the weight and speed of trains, as well as the quality of the ground. Typically, the ballast depth ranges from 9 to 12 inches, but it can be deeper in areas where the ground is unstable or where heavier trains operate.