It is very important to use suitable types of pipe joints while joining a pipe.
In this article, we will learn about the types of pipe joints used in the plumbing system.
Let’s get started!
There are various types of pipe joints are used in plumbing systems. The selection of pipe joints depends on some factors such as the size of the pipe, material of the pipe, the pressure of flow in the pipe, etc.
Different types of pipe joints used in the plumbing system are given below:-
- Threaded joint
- Soldered joint
- Grooved joint
- Flanged joint
- Welded joint (Butt weld & socket weld)
- Brazed joint
- Compression joint
- Push-fit joint
- Hep2o joint
Let us discuss these types of pipe joints in detail.
Table of Contents
1. Threaded Joint in Pipes
In this type of joint, two pipes are connected with a screw mechanism. Both pipes are threaded at their end. One pipe has threads on the external surface while the second one has threads on its internal area.
This type of pipe joint can be used for various types of pipes such as Galvanised Iron (G.I.) pipes, Poly Vinyl Chloride (PVC) pipes, cast iron pipes, and copper pipes.
The main drawback of threaded pipes is that they can be used where there is a low temperature and pressure. Threaded pipes are not suitable for high pressure and temperature.
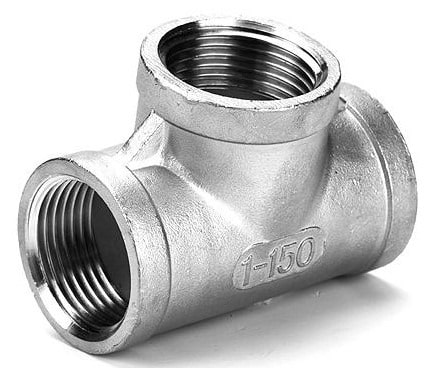
2. Soldered Joint in Pipes
In this type of pipe joint, two different metals form a single element by melting the two metals above 600 degrees Fahrenheit which cools down to form a strong electric bond, which is called soldering.
In soldered joints, the pipes are to be connected together with metal at a minimum temperature of 600 degrees Fahrenheit. When these pipes are cooled down, it creates a strong bond.
These types of joints are normally used in copper pipes. Skilled workers are needed for soldering work.
Soldering joints are usually done in copper pipes & copper alloy pipes. For soldering the pipes trained laborers are required. The soldered joints have lower mechanical strength, comparatively.
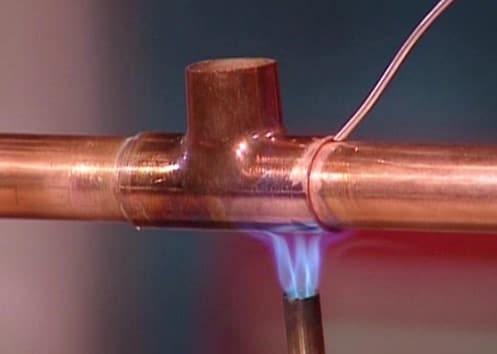
3. Grooved Joint in Pipes
In this type of pipe joint, the groove is provided at the end of the pipes. Grooves are created by using a grooving machine.
The rubber gasket is given over the ends of two pipes. Two-part coupling is provided around it using bolts and nuts.
The rubber gasket is used to prevent any air leakage and liquid leakage. Rubber gasket makes these pipes watertight and airtight. Two parts coupling is designed in such a way so that they can easily fit in the groove, which locks the pipes mechanically.
It is a very ancient technology and is widely used throughout the world. The main advantage of the grooved joint is that is very simple to join two pipes together.
Maintenance is also easy and fast due to the easy installation process. Grooved joints are most commonly used in fire-fighting pipe systems.
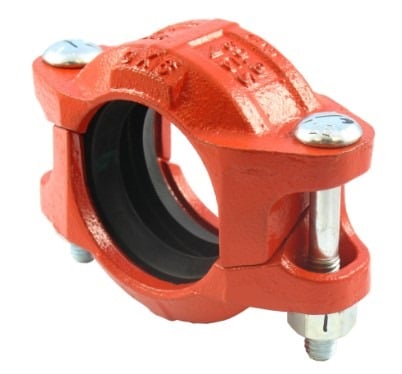
4. Flanged Joint in Pipes
The flanged joint is provided where pressure is very high. Normally it is used where the diameter of the pipe is large.
The flanged joint is a system of pipes, valves, pumps, and other equipment with the help of the flange method. A flange can be welded or screwed.
A rubber gasket is fitted between the two flanges to prevent any water leakage.
The flanged joint must be properly fixed with the help of skilled workers otherwise the system may get damaged due to high pressure in the pipe.
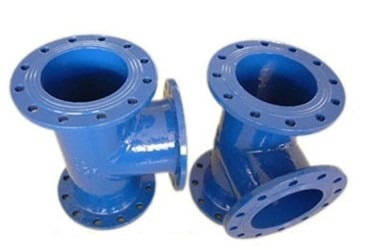
5. Welded joint (Butt weld & socket weld)
There are two types of joints used in the piping systems.
- Butt welded joint
- Socket welded joint
I. Butt welded joint
This type of joint is used when the pipes of similar diameters are to be joined with each other. Butt-welded joints are very popular pipe joints. The main advantage butt welded joint is that It provides good strength for the joint and is capable of resisting a high intensity of pressure. Skilled workers are needed to join the pipes using the butt welding technique. These types of joints are utilized for commercials and industrial systems of piping.
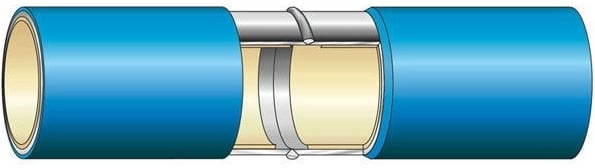
II. Socket welded joint
If two pipes are of different diameters then a socket welded joint is provided. One end of the pipe having a smaller diameter is inserted into an end of the pipe having a larger diameter. Thereafter, it welded around the joint.
A socket welded joint is used when there is more probability of leakage from the pipe joints. The cost of socket welded joints is normally lower than the cost of butt welded joints. So, it is more economical compared to the butt welded joints.
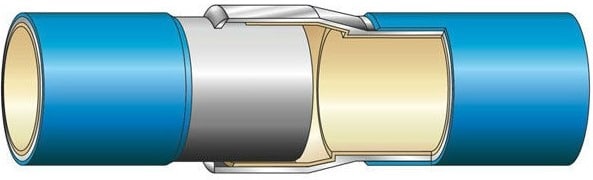
6. Brazed Joint in Pipes
These joints are very similar to soldered joints. The brazed joint is normally used to obtain higher joint strength. Brazed joints are constructed using the molten filler material, melted above 840 degrees Celsius. This filler material used is to give good affinity towards copper. Normally, brazing is done on copper pipes and copper alloy pipes.
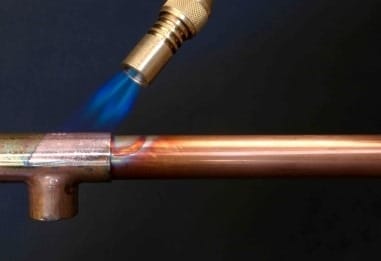
7. Compression Joint in Pipes
This type of joint is used where we have to connect two pipes of different diameters and the same or different materials. Both sides of the pipes should be plain to provide a compression joint. In this type of joint, a fitting or a threaded coupler is fitted and the pipes are joined using the coupler.
Compression fittings are available in different types of materials, which are used as per the requirements and types of pipes used to make compression joints.
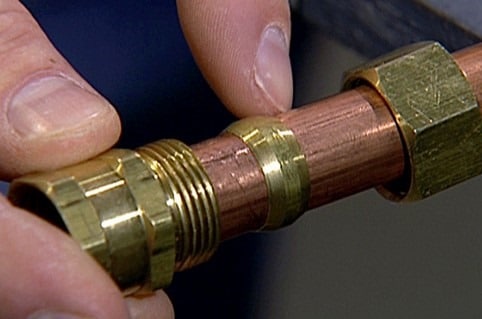
8. Push-Fit Joint in Pipes
This type of joint normally consists of a toothed ring for purpose of gripping the pipe and a rubber ring of ‘O’ shape which works as a seal, to stop any leakage in the pipe.
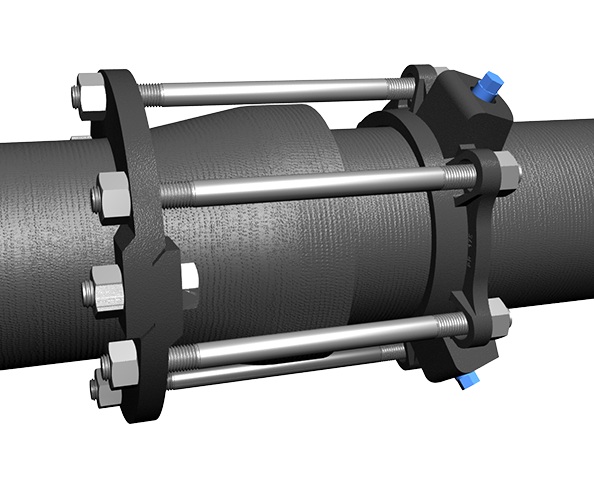
10. Hep2o Joint in Pipes
This kind of joint is basically the same as the compression joint. The Hep2o joints are explicitly intended for their utilization with polybutylene pipes. To join, the pipe is driven into the joint till it hits the pipe and that is it. Hep2o joints are more costly as compared with some other sort of pipe joint.
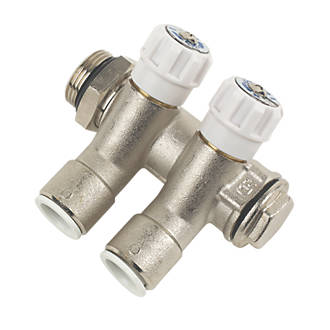