Table of Contents
Introduction Of HDPE Pipe
HDPE pipe, also known as high-density polyethylene pipe, is a flexible plastīic piping solution that is commonly used to replace older, aging concrete or steel main pipelines. This type of pipe is known for its high level of impermeability and strong molecular bond, making it suitable for use in high pressure pipelines. The versatility of HDPE pipe makes it suitable for a wide range of applications across the globe, including water mains, gas mains, sewer mains, slurry transfer lines, rural irrigation systems, fire system supply lines, electrical and communication conduit, and stormwater and drainage pipes. Overall, HDPE pipe is a durable and reliable solution for a variety of pipeline needs.
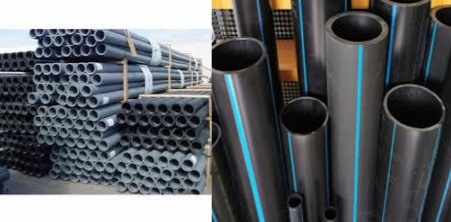
Description
HDPE pipe is a type of plastic pipe that is commonly used in fluid and gas piping systems. It is strong, durable, and resistant to chemicals and corrosion. It is also lightweight and easy to install. HDPE pipe can be joined together using various methods, including welding. This creates a strong and leak-free connection. HDPE pipe is also resistant to root intrusion, which can be a problem with other types of pipes. HDPE pipe is commonly used for water mains, fire ring mains, sewer mains, and gas mains pipelines. It is also used for electrical and telecommunications conduits. HDPE pipe is flexible and can be bent on site, making it easy to install. It is also resistant to chemicals, which makes it useful in process plants or around corrosive or acidic environments. HDPE pipe is safe to use for drinking water, as it is made from food-grade polyethylene. Overall, HDPE pipe is a cost-effective and long-lasting option for many different types of piping systems.
Manufacturing Process Of HDPE Pipe
High-density polyethylene (HDPE) pipe is a versatile and durable material that is widely used in a variety of piping systems. The manufacturing process of HDPE pipe involves the use of heat and extrusion to shape the raw material into a desired size and shape. In this article, we will take a closer look at the process of making HDPE pipe and the different factors that influence the final product.
The first step in the manufacturing process of HDPE pipe is the heating and extrusion of the HDPE resin. The resin is heated to a high temperature, typically around 180 degrees Celsius, and then extruded through a die. The die determines the diameter of the pipeline, while the wall thickness is determined by the size of the die, the speed of the screw, and the speed of the haul-off tractor.
After being extruded, the pipe enters cooling tanks where it is submerged or sprayed with water to cool and harden the material. The cooling process is done in stages to avoid deforming the shape of the pipe. Once cooled, the pipe is then passed through a laser or powder printer to print the size, type, date, and manufacturer’s name on the side of the pipe. The pipe is then cut into lengths or coiled on a coiler.
HDPE pipe is usually black in color due to the addition of 3-5% carbon black to the clear polyethylene material. This addition of carbon black makes the product UV light resistant. Other colors are available but are less common. Colored or striped HDPE pipe is usually 90-95% black material, with just a colored skin or stripe on the outside 5%.
A different die is used for striped HDPE pipe, which has small channels that the colored material runs through, just before it is pushed through the die. This means the stripes are formed as an integral part of the pipe and are not likely to separate from the main pipe body. Co-extruded, or co-ex HDPE pipe, has a second extrusion screw which adds an extra skin of color around the black HDPE pipe, this allows the pipe to be colored on the outside, for identification or thermal cooling requirements.
The manufacturing process of HDPE pipe is a complex process that involves the use of heat and extrusion to shape the raw material into a desired size and shape. By understanding the different factors that influence the final product, manufacturers can produce high-quality HDPE pipes that are durable and long-lasting. With its versatility and durability, HDPE pipe is widely used in a variety of piping systems and has become an essential material in many industries.
Applications Of HDPE Pipes
HDPE pipe, made from high-density polyethylene, is used in a variety of applications across the globe. Some common uses include:
- Water mains for the transportation of potable water
- Gas mains for the transportation of natural gas
- Sewer mains for the transportation of wastewater
- Slurry transfer lines for the transportation of mining tailings
- Rural irrigation for crop irrigation systems
- Fire system supply lines for the transportation of water in fire suppression systems
- Electrical and communications conduit for the protection of electrical and communication cables
- Stormwater and drainage pipes for the management of stormwater runoff.