Estimates suggest that the production of traditional cement accounts for around eight to ten percent of the world’s total emissions of carbon dioxide. This is because the process of crushing and heating limestone and clays to produce cement requires a substantial amount of energy and emits large amounts of carbon dioxide.
Engineers can reduce the environmental impact of their construction projects and contribute to global efforts to mitigate climate change by adopting green concrete, which uses sustainable materials and manufacturing processes such as recycled aggregates or industrial waste products, significantly reducing its carbon footprint.
Table of Contents
What Is Green Concrete?
Green Concrete is made from concrete waste. Green concrete is a very environmentally friendly concrete that utilized less energy in its production process.
The fact behind the name green concrete is that extra steps are taken in the mix design process of concrete and placement to ensure a sustainable structure and a long life cycle with a low maintenance surface.
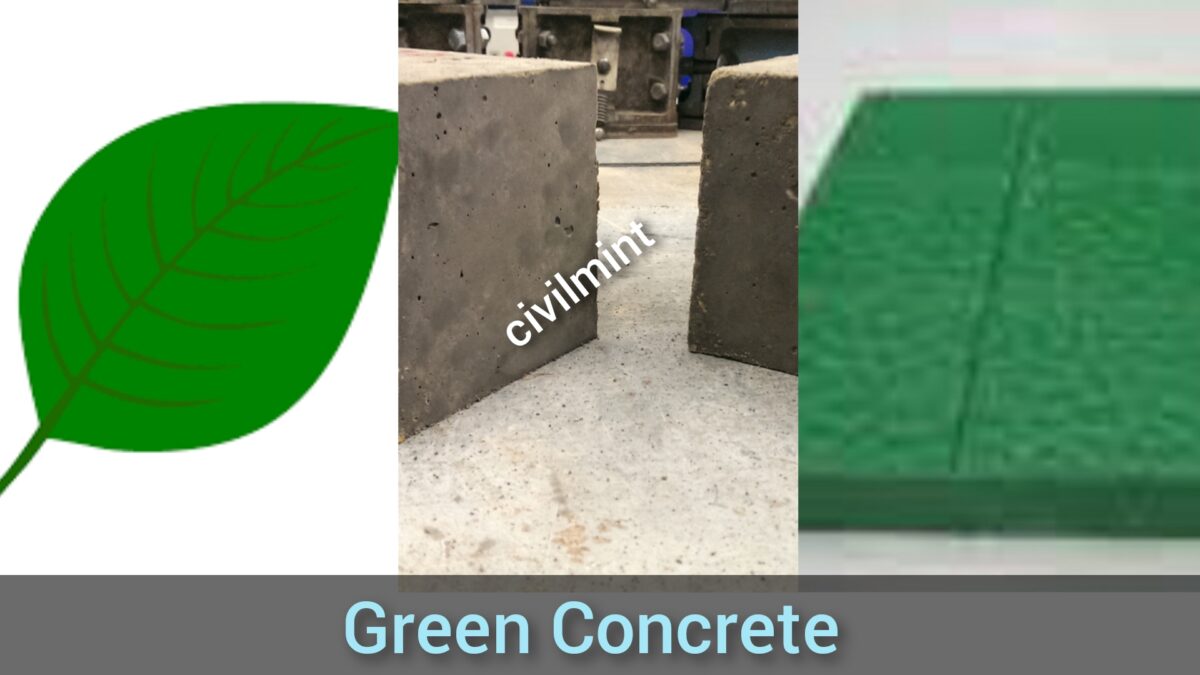
Green concrete does not represent only color but also represents the environment, which is surrounding us. It has been a very popular topic in the history of the concrete industry.
This was first developed in Denmark in the year 1998 by Dr.WG. It was made of Concrete wastes like slag, power plant wastes, recycled concrete, mining and quarrying wastes, waste glass, incinerator residue, red mud, burnt clay, sawdust, combustor ash, and foundry sand.
The primary objective of the Center for Green Concrete is to diminish the ecological effect of concrete. To empower this, new innovation is created in the form of green concrete. The innovation considers all phases of a concrete construction’s life cycle, i.e. structural design, specification, manufacturing, and maintenance, and it includes all aspects of performance.
By using Green Concrete omission of Carbon Dai Oxide can be reduced up to 21% compared to conventional concrete.
Materials Used In Green Concrete:
- Demolished waste aggregates of concrete buildings.
- Waste concrete.
- Blast furnace slag.
- Sand.
- Glass aggregates.
- Fly ash.
- Stainless steel oxidizing slag (SSOS).
Let us know in detail.
1. Demolished waste aggregates of concrete buildings:
These are recycled concrete aggregates (RCA) that are obtained by crushing and reusing waste concrete from demolished buildings or structures. The use of RCA in concrete reduces the amount of waste generated from construction activities and also conserves natural resources by reducing the need for virgin aggregates.
2. Waste concrete:
This refers to the excess or unused concrete that is generated during construction activities. This waste can be recycled and used as RCA in new concrete, thereby reducing the amount of waste generated and conserving natural resources.
3. Blast furnace slag:
This is a byproduct of iron and steel manufacturing processes. When used in concrete, it can improve the durability and strength of the concrete and also reduce the amount of cement needed, which in turn reduces the carbon footprint of concrete.
4. Sand:
Sand is a common ingredient in concrete and is used as a fine aggregate. However, the extraction of sand from rivers and beaches can cause environmental damage. To make green concrete, it is important to use sustainable sources of sand, such as desert sand or recycled glass.
5. Glass aggregates:
Recycled glass can be used as an alternative to sand as a fine aggregate in concrete. The use of glass in concrete reduces the demand for natural resources and diverts waste from landfills.
6. Fly ash:
This is a byproduct of coal-fired power plants. When used in concrete, it can improve the workability, durability, and strength of the concrete. The use of fly ash in concrete also reduces the amount of cement needed, which in turn reduces the carbon footprint of concrete.
7. Stainless steel oxidizing slag (SSOS):
This is a byproduct of stainless steel manufacturing. When used in concrete, it can improve the compressive strength and durability of the concrete. The use of SSOS in concrete reduces the amount of waste generated from manufacturing processes and also reduces the carbon footprint of concrete.
Advantages of Green Concrete:
- The emission of Co2 can be reduced by up to 21%.
- Less energy required to produce Green concrete.
- Utilization of waste material.
- Use of materials that can harm the environment.
Disadvantages of Green Concrete:
- Low durability.
- Cost is high due to the use of stainless steel oxidizing slag (SSOS).
- Can buckle easily due to the application of tensile load.
Applications And Uses
- Green concrete reduces the overall carbon footprint of a construction project.
- Manufacturers make green concrete from recycled materials, fly ash, and cement, and use it in both new construction and renovation projects.
- Green concrete has a much lower carbon footprint than traditional concrete, making it an ideal choice for infrastructure projects that require a large amount of concrete.
- Green concrete is lightweight, making it easier to install on rooftops or in other places where heavy loads would be difficult to place or move.
- The excellent insulating properties of green concrete help to reduce heating and cooling costs.
- The porous texture of green concrete allows moisture to dissipate into the ground instead of becoming trapped, making it an ideal choice for buildings that require insulation.
- Using green concrete is an economical choice because it uses recycled materials, which reduces the cost of raw materials. It also minimizes pollution and waste and can be considered a sustainable construction material that can help reduce the carbon footprint of construction projects.