Table of Contents
What is Hyperbaric Welding?
Hyperbaric welding is a high pressure welding. If it is done in dry environment, it is called hyperbaric welding. If it is done in wet environment, it is known as underwater welding. This type of welding is very famous in offshore oil-gas fields. Steel is used as a welding material.
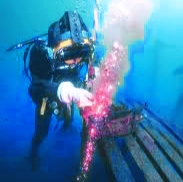
Underwater welding is a risky job. Highly skilled worker can only perform this job. Proper planning and job safety analysis is needed before performing welding operation.
Underwater welding should be done perfectly, otherwise, it is very difficult to repair welding defects.
How to Perform Hyperbaric Welding?
In dry welding, a high pressure chamber is sealed around the structure to be welded. The chamber is then filled with a gas. This gas consist of oxygen and helium. Water is evacuated to create a dry atmosphere for welding to occur. The chamber must be pressurized to an adequate level to prevent decompression sickness during welding operations.
Wet welding relies on releasing air bubbles around the arc to shield the weld and prevent electricity from passing through the water. This layer of foam insulation protects the diver, but obscures the weld area and makes it more difficult to complete the weld properly. Air bubbles can also disturb the weld pool and cause rapid cooling of the weld joint due to heat dissipation by the surrounding water. This increases the risk of defects such as cracks.
Risk Associated with Hyperbaric Welding
Underwater welding hazards include the risk of electrocution to the welder. To prevent this, the welding equipment must be adapted to the marine environment, properly insulated and the welding current must be controlled.
Commercial divers must also consider the occupational safety issues faced by divers, particularly the risk of decompression sickness due to increased breathing gas pressure. Many divers report a metallic taste associated with galvanic degradation of dental amalgams.
There may also be long-term cognitive and musculoskeletal effects associated with underwater welding.
Uses
- Underwater steel structures.
- Marine and ship welding.
- Offshore oil and gas fields.
- Underwater oil & gas pipelines.
- Structures built across river and canals.
- Nuclear power plants.
Sum Up
Underwater welding can be divided into dry welding and wet welding. Dry welding, which uses a high pressure chamber to create a dry environment around the weld area in which the welder can work, is superior to wet welding, which uses air bubbles created by a shielding gas to cover the area weld. yield results.
Underwater welding is a lucrative and essential profession, but it is also a dangerous one. The techniques used in underwater welding are used to repair offshore structures and equipment such as offshore pipelines, oil rigs, and ships. Underwater welding machines are also used in nuclear power plants.