Today I am going to explain very interesting welding topic called Thermite welding.
Let’s start!
Table of Contents
What Is Thermite Welding?
Thermite Welding, known also as exothermic bonding or thermit welding, stands as a welding methodology that achieves enduring conductor connections through the use of molten metal.

This welding process employs the inherent exothermic reaction of a thermite composition, thus eliminating the need for external heat sources or electrical currents. The pivotal chemical interaction involves aluminum powder and a metal oxide, generating substantial heat energy.
This elevated heat leads to the creation of molten metal, enabling the formation of strong and durable unions between the connected components.
Purpose Of Thermite Welding
Thermite welding offers superior mechanical strength compared to alternative welding methods. This technique boasts exceptional corrosion resistance and stability under repetitive short-circuit pulses. Moreover, it maintains consistent electrical resistance throughout its lifespan.
However, it’s important to note that thermite welding is a pricier process in contrast to other welding techniques. The procedure necessitates replaceable molds, and its repeatability can be limited. Additionally, unfavorable conditions such as wet weather can hinder the process when performed outdoors.
Thermite Welding Reaction
If I talk about in simple words, thermite welding is a method for joining metals using a chemical reaction that produces heat. In this process, aluminum dust is utilized to reduce metal oxides, such as iron oxide (Fe2O3), owing to aluminum’s high reactivity.
See the chemical reaction as given below.
Fe2O3 + 2 Al → 2 Fe + Al2O3
In this chemical reaction, aluminum oxide (Al2O3), elemental iron (Fe), and a substantial amount of heat are generated.
The standard mixture comprises five parts of iron oxide red (rust) powder and three parts of aluminum powder, which are ignited at high temperatures. This initiates a strongly exothermic reaction, leading to the creation of molten iron and refractory aluminum oxide slag. This mixture is commonly used for welding railway rails.
To enhance the quality of the weld, preheating is performed on the rail ends, and small pellets or rods of high-carbon alloying metal are added to the thermite mix. The alloying materials melt during the thermite reaction, blending with the weld metal. This process ensures sound railroad welds and the proper properties of the joined metals.
The reaction is activated using a spark or a hot flame, and sometimes a “booster” material like powdered magnesium is used to kick-start the reaction. The aluminum oxide slag produced in the process is discarded.
For welding copper conductors, a semi-permanent graphite crucible mold is employed. The molten copper produced by the reaction flows through the mold and forms an electrically conductive weld around the conductors. Hand-held graphite crucibles can also be used for this purpose. These crucibles offer advantages like portability, cost-effectiveness, and flexibility, making them suitable for various applications, including field work.
Thermite Welding Process
Preparation:
- Clean and prepare the metal parts to be joined.
- Place a mold or crucible around the joint area to contain molten metal.
Components and Mixture:
- Create a mixture using finely powdered metal (e.g., aluminum) and a metal oxide (usually iron oxide).
- Ensure accurate proportions for desired reaction and melting temperature.
Ignition:
- Initiate the exothermic reaction using a spark or igniter.
Exothermic Reaction:
- Trigger the reaction between metal powder (aluminum) and metal oxide (iron oxide).
- Generate intense heat, reaching temperatures up to thousands of degrees Celsius.
Melting and Bonding:
- Utilize the heat to melt the metal parts being joined.
- Achieve a unified pool of liquid metal.
Solidification:
- Allow the molten metal to cool and solidify.
- Form a strong, seamless bond between the metal parts.
Mold Removal and Finishing:
- Remove the mold or crucible.
- Clean off excess slag and address any imperfections.
Inspection:
- Inspect the welded joint for quality, strength, and durability.
- Ensure it meets specific standards before usage.
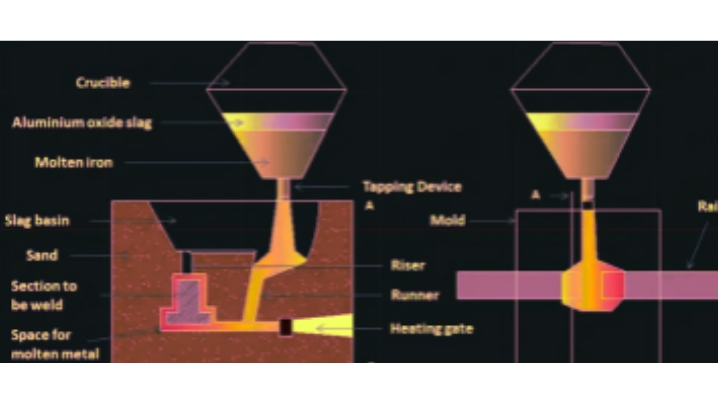
Applications Of Thermite Welding
- Thermite welding is versatile, capable of joining various metals including copper, stainless steel, cast iron, common steel, brass, bronze, and Monel. It excels at bonding dissimilar metals effectively.
- Widely used in electrical applications, exothermic welding is favored for creating dependable electrical connections for copper conductors. It’s particularly beneficial for grounding conductors and bonding jumpers as per the US National Electrical Code.
- The process finds extensive use in the railroad industry for welding track sections together. It ensures secure and robust joints, contributing to the durability and safety of the rail network.
- Thermite welding is employed in welding pipes and tubes, offering a reliable method to fuse metal components. Its ability to handle a range of metals makes it valuable for various pipe systems.
- Industries involving heavy machinery benefit from thermite welding for repairing and rejoining metal parts. Its stability and strength under demanding conditions make it suitable for maintaining industrial equipment.
Read also:
Conclusion
Thermit welding offers advantages such as strong welds with high mechanical strength and corrosion resistance. It remains stable over time, does not require external power, and is suitable for areas with limited power supply. However, it is expensive, requires replaceable molds, lacks repeatability, and cannot be used in wet or adverse weather conditions.