A Plate heat exchanger used various metal plates to transfer heat from one fluid to another fluid. These plates are positioned over each other. These plates are combined together so that fluid can move between them. The main advantage of plate heat exchangers over traditional heat exchangers is that when the liquid is exposed to a larger surface area, the liquid is dispersed throughout the plate. This improves the heat transfer coefficient and significantly accelerates the rate of temperature change.
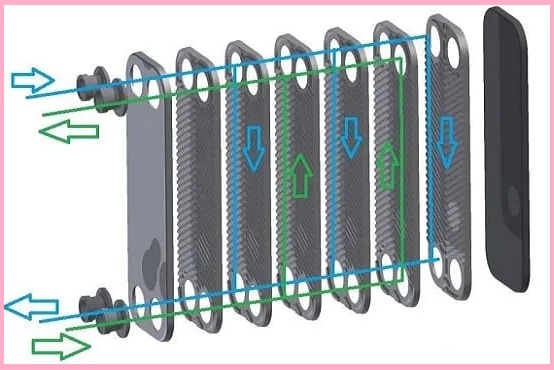
Plate heat exchangers are widely used today, with thousands of combi boilers used in the hot water sector in very small welded structures. High heat transfer efficiency at such a small size increases the flow of hot water in the combi boiler. The small plate heat exchanger has a great impact on home heating and hot water. Larger business models use gaskets between the plates, while smaller models tend to weld.
Table of Contents
Working Principal Plate Heat Exchanger
A plate heat exchanger is a type of heat exchanger that contains a series of metal plates for transferring heat between fluids. Plate heat exchangers operate according to the laws of thermodynamics. These exchangers have a hollow tubular shell defined on each plate. The
plate is arranged so that a thin rectangular channel is developed to exchange heat through the half piece. Working fluid travels between these winding, narrow channels. The plate of this heat exchanger is surrounded by a gasket to control the flow of fluid. These seals are arranged so that only one type of liquid (eg heated oil) spreads on one plate and another liquid (eg hot water) spreads on the next plate. The following figure shows two adjacent boards.
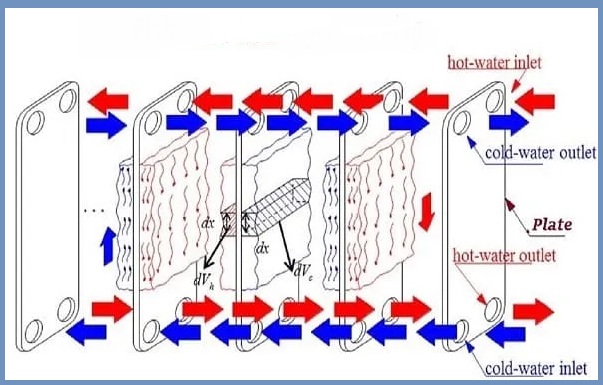
According to this arrangement, cold and hot liquids alternate through the plate, resulting in heat exchange. The slab has a large surface area. Therefore, it provides an excellent heat transfer coefficient as a shell and tube heat exchanger.
As you can see from the figure above, the coolant inlet (blue) is at the bottom, the coolant outlet is at the top, and vice versa, the hot liquid outlet (red). The cooled fluid flows upwards, the cooled fluid flows downwards, and heat is carried through the plate. After completion of this process, the heat medium is finally cooled and the cooling medium is heated. The heat transfer principle and plate heat exchanger design feature compact design, low heat loss, wide range of applications, flexible operation, high heat transfer efficiency, small footprint, convenient installation, and cleaning function.
Parts/Components of the Plate Heat Exchanger
The key components of plate heat exchangers are as follows:
- Plates
- Carrying beam
- Fixed Plate
- Support column
- Pressure Plate
- Guiding Bar
- Tightening Unit
- PHE Plates and gasket
See the below figure to understand it better.
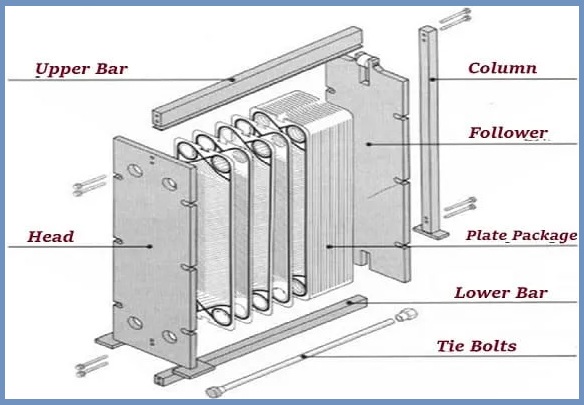
Types of Plate Heat Exchangers
- Gasketed plate heat exchangers
- Brazed heat exchanger
- Welded plate heat exchangers
- Semi-Welded heat exchanger
- Plate and Frame heat exchanger
Advantages of plate heat exchanger
- It has an easy layout.
- Design is simple.
- The rate of heat transmission is high compared to the shell & tube heat exchangers.
- There is no requirement for extra space.
- They have easy renovation and cleaning.
- The size is little compared to the shell & tube heat exchangers.
- Cheap installation cost.
Disadvantages of plate heat exchangers
- These heat exchangers have poor airtightness and are prone to leaks.
- Plate heat exchangers have higher flow resistance than tube heat exchangers.
- These have high-pressure drops. It has a high clogging index, especially suspended solids in liquids.
- The heat resistance of the sealant limits the operating temperature.
- Working pressure is limited and is usually less than 1.5MPa.
- Inadequate sealing can lead to leaks and difficult replacement.