Machining is the process in which we take a workpiece and give it a desirable shape and size by removing some amount of material from it. Whenever we talk about machining, especially in manufacturing, it’s very easy to think about metals and alloys only. But the material or workpiece which we can use for the machining process varies according to commercial and non-commercial purposes. It can be a composite material, ceramic material, wood, or even plastic. So, don’t be surprised when you see these kinds of materials are getting machined along with metals and alloys in the manufacturing sector.
So, in the machining process, we are removing some amount of extra material from the big chunk and making it useable by giving it a desirable shape. That’s why it is called ‘Subtractive Manufacturing’.
From the name itself, we can understand that in this process we are removing or subtracting the extra material from the workpiece. The removal of material in the machining process is done in a very highly controlled manner. This is why it is called the ‘controlled removing process’. The machine tools which remove the material are controlled accordingly. It only removes what is required, to give the workpiece a final shape. The material-removing tools are controlled so well that they neither remove extra material nor less from the workpiece. So, controlling the removing process play an important role in machining.
Table of Contents
Subtractive Manufacturing And Additives Manufacturing-
Subtractive and Additives manufacturing are opposite to each other. In subtractive manufacturing, we remove extra materials from the given workpiece to give it a final shape. As we have discussed, we do control removing in this kind of manufacturing process.
On the other hand, in additive manufacturing, we add extra material to make the final product. 3D printings are the best example of additive manufacturing. In 3D printing, we add materials to print the final product. Turning, drilling, milling, etc are good examples of subtractive manufacturing.
The advantage of additive manufacturing is that the final product will be as strong as the source material or workpiece. But the biggest disadvantage of this kind of manufacturing is that it produced tons of scraps and waste materials. While on the other side the advantage of additive manufacturing is that it doesn’t produce waste materials like subtractive manufacturing. But this process also has one disadvantage. The strength of the final product produced by this process may vary from the source material.
Types Of Machining Process-
- Turning process
- Drilling process
- Milling process
Turning Process:
Turning is the basic machining process. In this process, the material is removed from the outside of the workpiece. While doing the turning process the workpiece moves and rotates accordingly but the cutting tool remains stationary. Lathe machines are generally used for this process because it removes the material precisely.
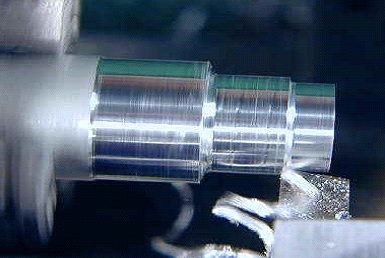
Drilling Process:
From the name itself, we can get an idea that this process is used for drilling or making a hole in the workpiece. The tools we use for drilling have a circular cylindrical shape and it rotates at high speed. When these drilling tools come into contact with the workpiece it starts removing the material in a circular shape and that’s how it creates a hole in the workpiece. It is estimated that most of the metal removing process is done by drilling only.
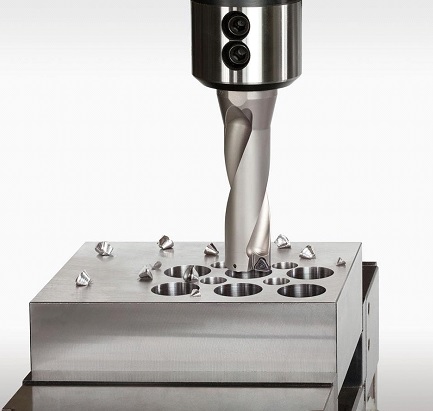
Milling Process:
In the milling process, the material is removed from the workpiece by the cutter which rotates at a very high speed. Sometimes certain workpiece needs to increase their drilled hole size. In this kind of situation, milling comes very handy. Milling can increase the drilled hole size by feeding the workpiece to the cutter. The milling process is generally considered less accurate than the other machining process.
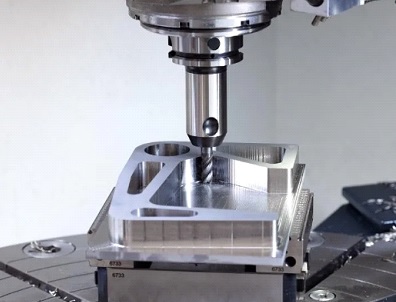