(Concrete slab casting procedure | RCC slab casting procedure)
Table of Contents
Introduction Of RCC Slab Casting
In this article, we will talk about the concrete slab casting procedure. Concrete slabs are strong and sturdy structures that are commonly used in building construction. They provide a solid foundation for buildings, roads, and other structures.
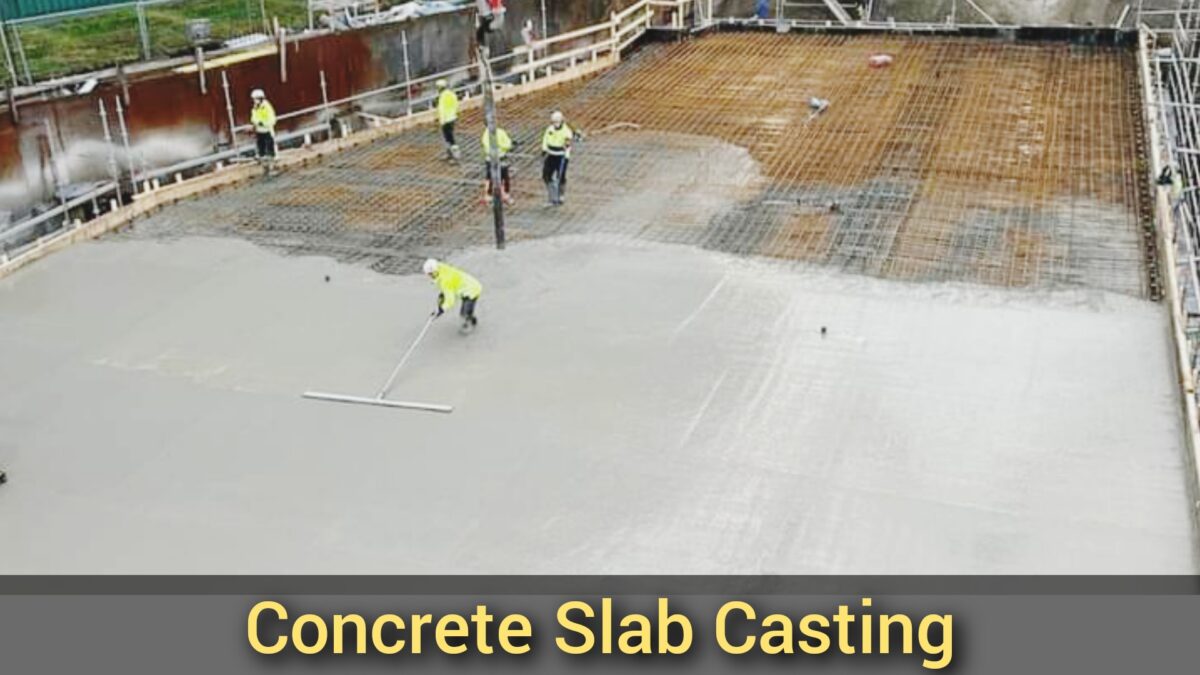
Let us know the steps involved in casting a concrete slab.
Materials Needed
Before we start casting a concrete slab, we need to collect the following materials for execution Of smooth work on construction site.
1. Concrete mixture:
A special mixture of cement, sand, and gravel that will harden into a solid slab.
2. Wooden boards:
These are used to create a frame or mold for the slab.
3. Reinforcement bars:
These are metal bars that are placed inside the concrete to make it stronger.
4. Nails and a hammer:
These are used to secure the wooden boards together.
5. Water:
Water is added to the concrete mixture to make it workable.
6. Shovel:
A shovel is used to mix the concrete and move it around.
I would recommend you to read my article on heavy construction equipments.
7. Level:
A tool that helps ensure the slab is even and level.
8. Trowel:
A tool used to smooth and finish the surface of the slab.
Slab Casting Procedure
1. Prepare the site:
Choose a suitable location for the slab. Clear the area of any debris or vegetation. Make sure the ground is level and compacted.
2. Build the formwork:
Take the wooden boards and nail them together to create a rectangular frame. Make sure the frame is the desired size and shape of the slab. Use a level to check that the formwork is even.
3. Place the reinforcement bars:
Inside the formwork, lay down the reinforcement bars in a crisscross pattern. These bars will make the slab stronger and prevent it from cracking.
4. Mix the concrete:
In a mixing container, combine the cement, sand, gravel, and water. Use the shovel to mix them thoroughly until you get a smooth, workable consistency.
5. Pour the concrete:
Carefully pour the concrete mixture into the formwork. Start from one end and work your way to the other, ensuring that the entire area is evenly filled. Use the shovel to spread the concrete and fill any gaps.
6. Level the surface:
Use a screed or a flat piece of wood to level the surface of the concrete. Move it back and forth in a sawing motion while applying slight pressure. This will remove any excess concrete and create a smooth, even surface.
7. Finish the surface:
Once the concrete is leveled, use a trowel to smooth and finish the surface. Gently glide the trowel over the concrete, pressing down to remove any imperfections or air bubbles. This will give the slab a nice, polished look.
8. Curing and drying:
After finishing the surface, allow the concrete slab to cure and dry. This process may take several days or weeks, depending on the weather conditions. During this time, it is important to protect the slab from excessive moisture and keep it covered.
9. Remove the formwork:
Once the concrete is completely dry and hardened, carefully remove the formwork. Start by removing the nails and then gently pull the wooden boards away from the slab. Be cautious not to damage the edges of the slab.
Conclusion
Careful planning and execution are involved in casting a concrete slab. By following the steps outlined in this blog, you have learned how to create a strong and durable concrete slab.
Always work with engineer supervision and take safety precautions when working with concrete. With practice and patience, you can become skilled in the art of casting a concrete slab.
I hope you liked my article on “concrete slab casting procedure”.
Faqs
The steps in RCC slab casting include preparing the formwork, placing reinforcement bars, pouring the concrete, compacting it, and allowing it to cure.
The ideal thickness of an RCC slab depends on factors such as the load it will bear and the span it needs to cover. Generally, residential slabs have a thickness of 4 to 6 inches, while commercial or industrial slabs can range from 6 to 8 inches or more.
To prevent cracks in an RCC slab, it is important to properly design the reinforcement layout, provide adequate concrete cover to the reinforcement, control the water-cement ratio, and ensure proper curing of the slab after casting.
Casting an RCC slab in rainy weather is not recommended as excessive moisture can affect the quality and strength of the concrete. It is best to wait for dry weather conditions to ensure a successful casting.
The formwork should be left in place for a sufficient period to allow the concrete to gain strength and support its own weight. Generally, the formwork is removed after 2 to 3 days for vertical elements like walls, while for horizontal elements like slabs, it is removed after 7 to 14 days, depending on the curing process and structural requirements.