High Performance Concrete is a type of strong and durable concrete that is made with special ingredients and techniques. It is used to build structures that can handle more weight, last longer, and require less maintenance.
Table of Contents
What Is High Performance Concrete?
High performance concrete is more durable and has higher strength compared to conventional concrete. It is made by using the same materials as traditional concrete but it is designed in such a way that it can gain more strength. The compressive strength of high-performance concrete is more than is 55 MPa or more.
How To Achieve High Performance Concrete
By using low water/cement ratio, pozzolanic materials, by improving transition zone strength, packing aggregates densely high performance of concrete can be achieved.
For Workability which is needed for a particular construction, superplasticizers are used to reduce water content by scattering cement particles. Regarding pozzolanic materials, it enhances concrete strength and thereby reduces its permeability.
Low permeability decreases the acceptance of aggressive substances and improves concrete durability. Both requirements of low permeability and high strength are connected with each other by the need to decrease the volume of comparatively bigger capillary pores.
The decrease of capillary pores is feasible by a low water and cement ratio and also dense packing of fine particles.
What Is The Mechanism Of High Performance Concrete?
There are some ways to achieve high-performance concrete as follows.
- By using Pozzolanic Materials or Mineral Admixtures
- Compact Packing of Concrete Components.
- By using Superplasticizers
- Transition zone improvement
Let us discuss the above-mentioned methods in detail.
1. Pozzolanic Materials or Mineral Admixtures
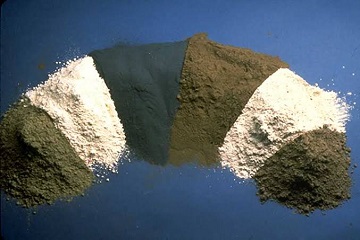
Silica is a pozzolanic material and its role is abundant due to the large surface area and comparatively good content of glassy silica, which is very reactive.
The impact of Silica fume on the strength of concrete is outstanding. To replace 60 kg of cement to get the comparatively same amount of compressive strength, a small amount of silica i.e 20 kg will be much.
Silica fume would increase the early strength of concrete and the heat of hydration decreases. In mass concrete silica, fumes are considered advantageous because of their high property.
2. Compact Packing of Concrete Components
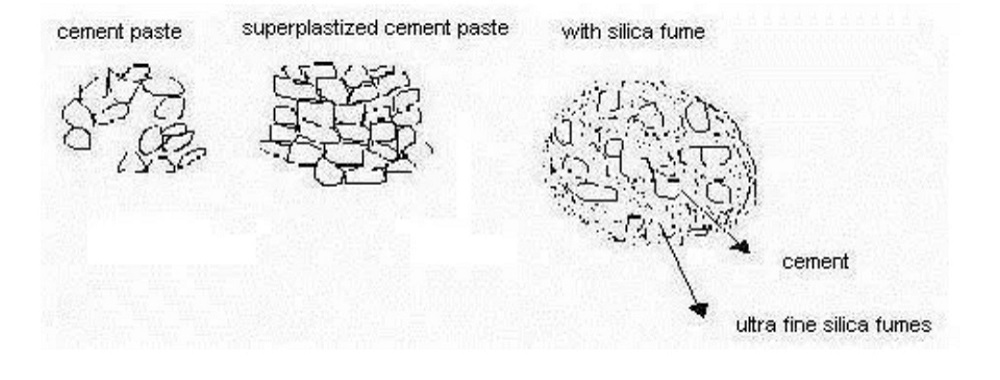
To obtain high-performance concrete, compact packing is another technique. Cement particles are dispersed by superplasticizers. Silica fume pozzolanic materials can fill the space between particles of dispersed cement and simply packed fine and coarse aggregate.
And we get a denser microstructure as an overall result. Less porosity is shown by concrete with no indication of capillary pores, and an electron microscope with very less 0.5 mm gel pores is visible. The above image shows the cement packing that contains silica fumes and superplasticizers.
3. Superplasticizers
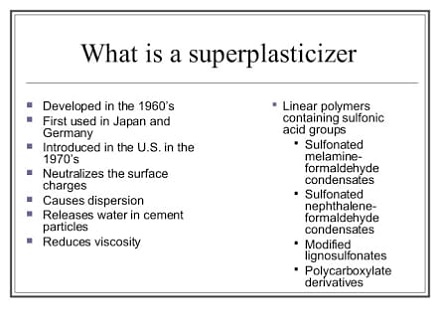
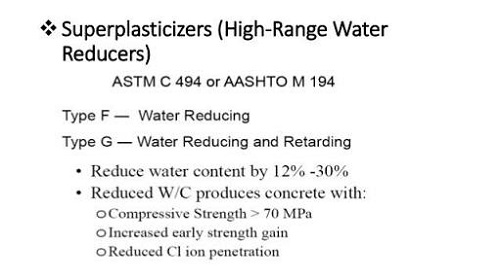
Superplasticizers’ functions are to reach cement granules to pass on the negative charge on them. And after that cement granule gets deflocculated and disperse. This dispersion of cement granules improves concrete workability. And this can make concrete capable to flow for the water to cement ratio, or decrease in water content for the same workability. Superplasticizers are long-chain molecule organic compounds.
4. Enhancement of Transition Zone
Improvement in the strength of the transition zone in concrete is another important procedure to get high-performance concrete. With the presence of silica fumes, dense Calcium Silicate hydrate (C-S-H) occupies all the space around aggregate and established a direct bond with aggregate.
As a result of the strengthened transition zone, there is a reduction in micro-cracking at the interface between aggregate and cement paste.
Advantages Of High Performance Concrete
- High performance concrete has higher strength than conventional concrete.
- Its dense microstructure and low porosity make it more durable and resistant to weathering, corrosion and chemical attack.
- High-performance concrete has a low shrinkage rate, making it less prone to cracking.
- It can be designed to have a smooth, polished and even colored finish.
- High-performance concrete requires less maintenance than conventional concrete, resulting in less cost and inconvenience.
- Its use reduces the amount of material required, thereby reducing environmental impact and improving sustainability.
- It is highly adaptable and can be adjusted to suit specific construction requirements.
- It has a high level of fire resistance, which minimizes the spread of fire in the event of an accident.
- High-performance concrete is an excellent thermal insulator, which can help reduce energy costs in buildings.
- Its strength and durability can help improve the safety of structures in hazardous areas.
Disadvantages Of High Performance Concrete
- High-performance concrete can be costly due to the use of expensive materials and specialized construction techniques.
- This type of concrete is more prone to cracking under certain conditions than traditional concrete.
- High-performance concrete typically has a longer curing time and requires more complex placement and finishing techniques.
- The curing process of high-performance concrete is sensitive to changes in temperature and humidity.
- The installation and maintenance of high-performance concrete may require skilled labor that is not readily available.
- The reduced workability of high-performance concrete can make it more difficult to shape and place.
- High-performance concrete has a higher risk of shrinkage and creep, which can lead to structural problems over time.
- Due to its high density and viscosity, high-performance concrete is more challenging to mix and transport.
- There is a higher potential for alkali-silica reaction in high-performance concrete, which can cause concrete degradation.
- The production of high-performance concrete can be limited by the availability and variability of local sources for raw materials.
Applications Of High Performance Concrete
- High Performance Concrete can be used to build strong and long-lasting bridges that can hold up heavy cars and trucks.
- High Performance Concrete can be used to make tunnels that are really strong and won’t get damaged by water or chemicals.
- High Performance Concrete can be used to make tall buildings that are really strong but also lighter, so they can be built higher up in the sky.
- High Performance Concrete can be used to make dams that can hold back a lot of water without breaking.
- High Performance Concrete can be used to make special walls that can protect people from radiation and heat in nuclear power plants.
- High Performance Concrete can be used to make runways that airplanes can land on safely without causing damage.
- High Performance Concrete can be used to make walls near the ocean that can protect against big waves and salty water.
- High Performance Concrete can be used to make strong garages where cars can park without causing damage.
- High Performance Concrete can be used to make tanks that can hold lots of water without leaking or breaking.
- High Performance Concrete can be used to make big sports stadiums that are really strong and can hold lots of people.
Summary
High-performance concrete has high strength but it takes time to prepare. In normal construction work, conventional concrete is used.
High-performance concrete is normally used in the construction of tunnels, bridges, highway pavements, high rise building structures due to superior compressive strength, long-lasting, and high modulus of elasticity.
FAQS
Yes.
High Performance Concrete offers improved strength, durability, workability, and resistance to extreme weather and chemical exposure.
High Performance Concrete typically consists of cement, water, aggregates, and chemical admixtures.
High Performance Concrete has improved mechanical and durability properties compared to regular concrete due to the use of special materials and techniques.
High Performance Concrete can have a compressive strength of over 60 MPa.
Yes, High Performance Concrete is generally more expensive than regular concrete due to the cost of materials and specialized production methods.
High Performance Concrete is used in various construction applications, such as bridges, high-rise buildings, and infrastructure projects.
Yes, High Performance Concrete is well-suited for use in severe weather conditions due to its improved resistance to extreme temperatures and environmental exposure.
High Performance Concrete can last several times longer than regular concrete due to its improved durability and resistance to environmental exposure.
Yes, High Performance Concrete can be used for casting and offers improved workability compared to regular concrete, making it easier to handle during the casting process.