Table of Contents
What Is Ultra High Performance Concrete?
Ultra High Performance Concrete is an extremely strong and durable type of concrete. According to the American Concrete Institute (ACI) definition, Ultra High Performance Concrete has a minimum compressive strength of 150 megapascals (MPa) and specific requirements for durability, tensile ductility, and toughness.
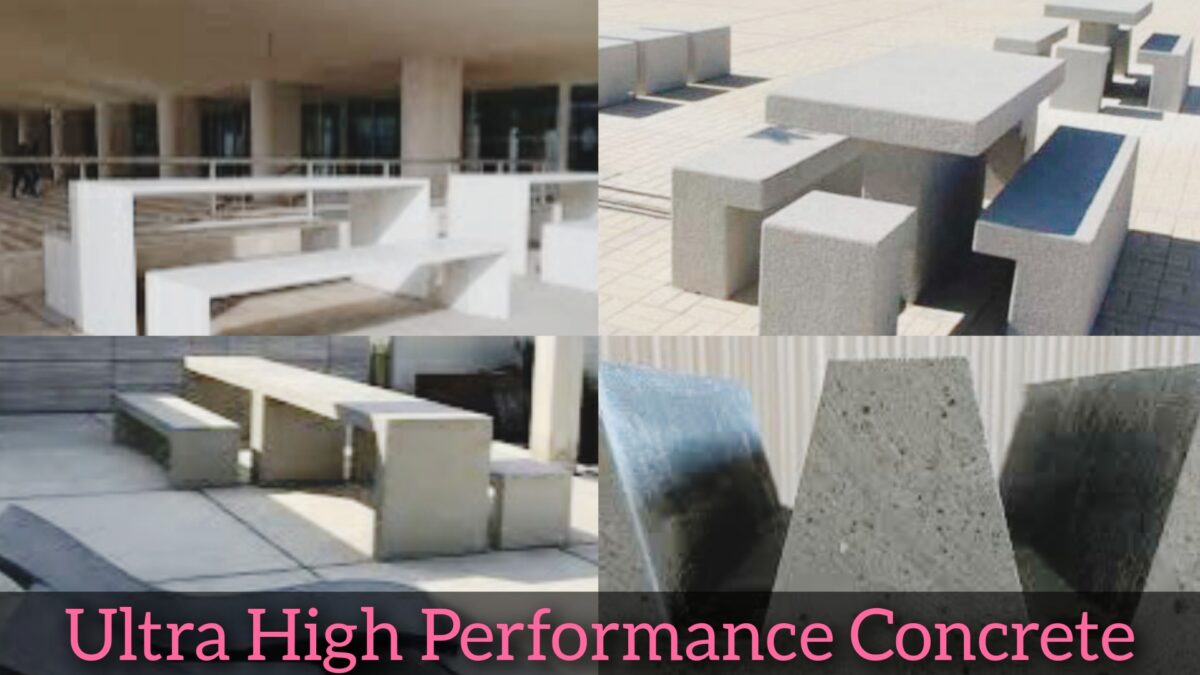
It achieves these properties by including materials such as cement, silica fume, fine quartz sand, high-range water reducing admixtures, and steel fibers.
The mechanical properties of Ultra High Performance Concrete are impressive. It has a compressive strength higher than 150 MPa, which means it can withstand heavy loads without breaking.
This type of concrete has sustained tensile strength even after cracking, with values greater than 5 MPa. This means it remains strong even if it develops small cracks, which enhances its durability.
One of the key benefit of Ultra High Performance Concrete is its superior durability compared to ordinary concrete. Ultra High Performance Concrete has discontinuous pores, which makes it harder for liquids to penetrate the material. This enhances its resistance to factors like moisture, chemicals, and freeze-thaw cycles, resulting in a longer service life for structures made with Ultra High Performance Concrete.
Because of its exceptional properties, Ultra High Performance Concrete finds applications in various civil engineering structures. It is commonly used in highway infrastructure projects and structural rehabilitation. By utilizing Ultra High Performance Concrete, engineers can address design challenges, improve the service life of structures, and reduce life cycle costs associated with the use of concrete.
Features Of Ultra High Performance Concrete
1. High strength:
Ultra High Performance Concrete is incredibly strong when it comes to resisting compression. It typically has a compressive strength ranging from 150 to 250 MPa, which is significantly higher than regular concrete that usually falls within the 20-40 MPa range.
2. Good Tensile strength:
Ultra High Performance Concrete demonstrates remarkable tensile strength, typically ranging from 8 to 12 MPa. This strength is achieved by adding steel fibers to the concrete mix, which enhance its ability to withstand cracking and provide flexibility.
3. High Durability:
Ultra High Performance Concrete is highly durable thanks to its low permeability and resistance to chemical attacks, freeze-thaw cycles, and abrasion. It is commonly used in applications where long-term performance is crucial.
4. Thin sections:
Ultra High Performance Concrete can be molded into thin sections without sacrificing its strength and durability. This makes it suitable for creating delicate architectural elements and lightweight precast components.
5. Precast applications:
Ultra High Performance Concrete finds extensive use in precast construction, where it is employed to manufacture structural elements like beams, columns, facades, and cladding panels. Its high strength allows for the reduction of material quantities and leads to more efficient designs.
6. Bridge construction:
Ultra High Performance Concrete is frequently employed in the construction of bridges due to its ability to create slender and lightweight bridge components with exceptional load-bearing capacity. This enables the construction of longer-span bridges while reducing the overall weight of the structure.
7. Impact resistance:
Ultra High Performance Concrete offers excellent protection against impact loads, making it suitable for applications that require resistance against blast or impact forces. These applications include security barriers, protective structures, and military applications.
Components Of Ultra High Performance Concrete
1. Cementitious Materials:
Ultra High Performance Concrete generally contains a combination of cementitious materials, which provide the binding properties.
This can include Portland cement, typically in the form of Type I or Type II cement, as well as supplementary cementitious materials like silica fume or fly ash. These materials enhance the strength and durability of the concrete.
2. Fine Aggregates:
Ultra High Performance Concrete incorporates fine aggregates such as sand, which contribute to the overall density and workability of the concrete. The sand used is typically well-graded and free from impurities to ensure optimal performance.
3. Silica Fume:
Silica fume is a highly reactive pozzolanic material that is commonly added to Ultra High Performance Concrete.
It is a byproduct of the production of silicon and ferrosilicon alloys. Silica fume improves the packing of particles, reduces porosity, enhances strength, and enhances the overall performance of the concrete.
4. Fibers:
Ultra High Performance Concrete often includes steel or synthetic fibers to enhance its tensile strength and toughness. Steel fibers, typically short and discrete, are commonly used to provide post-crack strength and improve the ductility of the concrete. Synthetic fibers, such as polypropylene or glass fibers, can also be added to enhance durability and reduce cracking.
5. Chemical Admixtures:
Various chemical admixtures may be added to Ultra High Performance Concrete to modify its properties. These can include superplasticizers to improve workability, water reducers to decrease the water content, accelerators to speed up the hydration process, and air-entraining agents to introduce controlled air voids.
6. Water:
Ultra High Performance Concrete requires a precise water-to-cementitious materials ratio to achieve the desired properties. The water used should be clean and free from impurities to prevent any adverse effects on the concrete’s performance.
Pouring And Curing
The pouring and curing process of Ultra-High Performance Concrete shares similarities with established procedures used for some High-Performance Concretes. The fluid mixture of UHPC is highly self-placing, eliminating the need for internal vibration. In the event that smooth flow is required, external form vibration can be utilized to facilitate proper placement.
After an initial setting period of 24 hours, the curing of Ultra High Performance Concrete requires an additional minimum of 48 hours, which includes subjecting it to a vapor bath maintained at a constant temperature of 88 °C. Consequently, Ultra High Performance Concrete can be ready for loading within three days, significantly reducing the time compared to the nearly 30 days required for conventional concrete to reach a similar state.
Advantages Of Ultra High Performance Concrete
1. Super Strong:
Ultra High Performance Concrete is incredibly strong and can handle heavy things without breaking easily.
2. Lasts Long :
Ultra High Performance Concrete stays strong and doesn’t get damaged quickly, so buildings made with it can last a really long time.
3. Doesn’t Get Hurt Easily:
Ultra High Performance Concrete doesn’t get damaged by things like water, chemicals, or bad weather, which means it can stay strong for a long time.
4. Doesn’t Break Easily:
Ultra High Performance Concrete can bend and handle things pushing on it without breaking easily. It can stay in one piece even when it’s being used a lot.
5. Looks Really Nice:
Ultra High Performance Concrete is very smooth and pretty to look at. It can be made into fancy shapes and designs, making buildings look beautiful.
6. Gets Built Quickly:
Ultra High Performance Concrete can get strong faster than regular concrete, so buildings can be built more quickly.
7. Stays Safe in Fires:
Ultra High Performance Concrete doesn’t get damaged easily by fire. It can handle high temperatures and keep buildings safe for a longer time.
8. Helps the Environment:
Ultra High Performance Concrete is good for the Earth because it lasts a long time, so we don’t have to use as much new material. It also helps us save energy because we don’t need to repair or replace things as often.
Various Applications Of Ultra High Performance Concrete
Ultra High Performance Concrete is used to make bridges and roads that can hold heavy cars and trucks. It is also great for places that have earthquakes or bad weather.
Ultra High Performance Concrete is used to make special parts for buildings. These parts can be very thin and light, but still strong and durable. They can also be shaped in cool and fancy ways.
Ultra High Performance Concrete is used to make walls and barriers that can withstand big explosions or crashes. It can absorb a lot of energy and keep people safe.
Ultra High Performance Concrete is used to fix old buildings that are falling apart. It can make them stronger and last longer. It can also be used in places where chemicals or rough things are present.
Ultra High Performance Concrete helps us take care of the environment. Since it lasts a long time and needs less maintenance, we don’t have to use as many resources or spend as much money.