Different types of flanges are used in the piping system. In this blog article, We will learn all the popular types of flanges used in the piping.
Table of Contents
1. Blind Flange
Blind flanges are manufactured without piercing and are used to seal the ends of openings in pipes, valves and pressure vessels to prevent liquid flow.

Blind flanges must withstand considerable mechanical loads caused by system pressures and screwing forces.
These flanges block the ship’s pipes or nozzles when not in use. Nozzles are often closed with blind flanges for system pressure checks or simply because the customer does not use all the nozzles specified for the tank. When fused with suitable gaskets, these flanges provide excellent sealing even under high temperature conditions.
2. Lap Flange
Lap flanges have flat faces and should always be used in conjunction with stub ends.

Unlike slip-on flanges, wrap flanges have a radius where the flange face meets the bore. This is so that the flanged portion of the stub end fits. Use bolts to attach the wrap flange to the stub end so that it can slide over the pipe. Because lap flanges can be made of inferior materials than stubs, lap flanges provide a reasonably priced mechanical connection and reduce the overall cost of a piping system.
For stainless steel or nickel alloy piping, the use of lap flanges in combination with stub ends is an economical option, as the material of lap flanges is of poor quality.
3. Long Neck Welded Flange
Long weld neck flanges are used primarily in the oil and gas industry under conditions of high pressure and high temperature. Long weld neck flanges are similar to standard weld neck flanges. However, the neck is much longer and acts like an extension bore.

Long weld neck flanges are commonly used to secure water mains or gas wells that are pumped into larger pipe networks such as those found in manufacturing facilities and homes.
4. Push-in Flange
A slip-on flange is a flange that is attached to a pipe or fitting by two fillet welds, one inside the flange cavity and one outside the flange.

A slip-on flange is a flange that slides over a pipe, hence the name. The bore size of the slip-on flange is larger than the outside diameter of the connecting pipe, so the pipe must be moved within the flange to join with a fillet weld.
A slip-on flange is a type of flange commonly used in liquid lines.
5. Threaded Flange
Threaded flanges are similar to slip-on His flanges, with the main difference being that threaded flanges are counterbored to fit the inner diameter of a particular pipe.

Threaded flanges save time and money and are ideal for small diameter piping systems. It is also the only choice for flanges in hazardous areas where welding is dangerous.
6. Weld Neck Flange
Weld neck flanges are also known as raised hub flanges or tapered hub flanges. Pressure build-up at the bottom of the flange can be reduced by using a weld neck flange with a neck that can transfer stresses in the pipe.
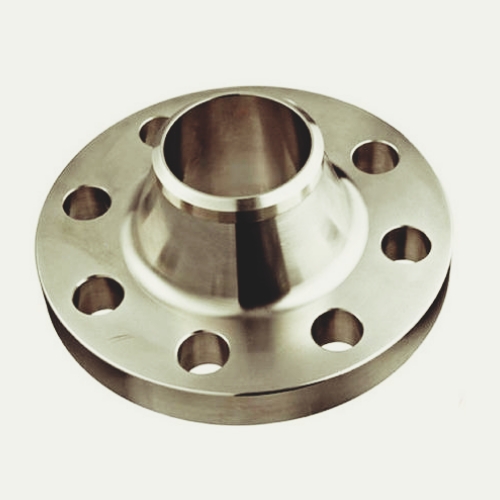
It works from high temperature to low temperature and is suitable for piping that can withstand high pressure. The diameter of the connected pipe should match the dimensions of the flange. A round fitting with an overhang edge all around forms a weld neck flange. Weld neck flanges have also been used effectively at pressures up to 5000 psi.
7. Socket Weld Flange
Socket weld flanges are joined to the pipe with a single fillet weld made on the outside of the flange. The pipe is inserted into the socket with a small gap so that the pipe is correctly positioned after the welding process.
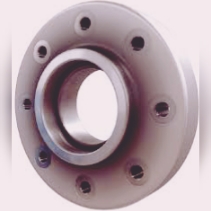
Socket weld bottom clearance is intended to minimize residual pressure that can build up in the weld root as the metal solidifies during the welding process. Socket weld flanges are suitable for compact high pressure piping systems carrying non-corrosive liquids.