A dynamic pump is a form of pump that supplies kinetic energy to the running fluid and will increase the fluid pace because it passes via the impeller and, then transforms this accelerated pace into pressure.
Dynamic pumps are also called kinetic pumps because they pump fluid by providing kinetic energy. This pump most commonly uses centrifugal force to pump fluid. Dynamic pumps are used in applications that require continuous flow. These pump types consist of an impeller, diffuser, and casing.
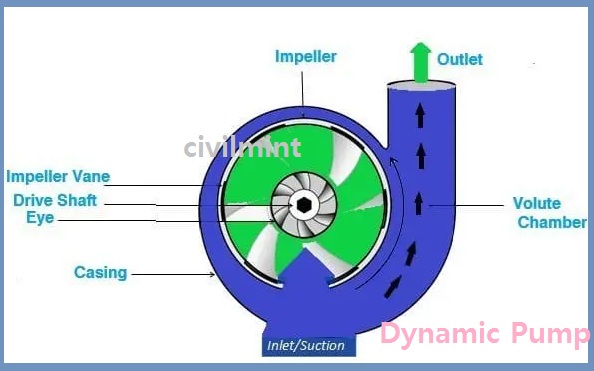
The main difference between dynamic pumps and positive displacement pumps is how they work. Dynamic pumps use rotating impellers to create cavities, and positive displacement pumps use reciprocating parts (such as pistons and plungers) to create cavities. The dynamic pump has fewer rotating parts than the positive displacement pump. Lighter than a positive displacement pump. Centrifugal and submersible pumps are the most common examples of dynamic pumps.
Table of Contents
How Does Dynamic Pump Work?
A dynamic pump is a kind of pump that utilized centrifugal force to move a liquid from one place to another. Rotating parts of the3 pump such as rotors, and impellers produce this centrifugal force.
As the liquid flows through the impeller, it adds kinetic energy to the liquid and increases its velocity. This fast fluid slows down the fluid and converts the fluid velocity into pressure energy as it passes through the vortex after passing through the impeller. After this process, the outlet valve opens and the liquid is distributed to the desired area.
Various Types of Dynamic Pumps
The most popular types of dynamic pumps are as follows:
- Submersible pump
- Centrifugal Pump
- Axial Pump
- Hydrant System
Let us have a look at these types of pumps.
1. Submersible Pump
A submersible pump is a mechanical device that works by pushing water to the surface rather than drawing it. It has a sealed motor that is linked to the pump body and helps push the liquid to the surface.
These types of dynamic pumps are most commonly used for sludge pumps, common industrial pumps, sewage pumps, septic tank pumps, and drainage.
2. Centrifugal Pump
Centrifugal pumps are a sort of dynamic pump that makes use of centrifugal pressure to transform mechanical energy into hydraulic energy. The energy transformation is executed with the aid of using the 2 foremost additives of the pump, the volute casing, and the impeller. The foremost cause of the volute is to accumulate the fluid leaving the impeller and convert the rate of the fluid into strain energy.
These dynamic pumps are maximum generally used to pump drinks from low heads to excessive heads. These dynamic pumps are utilized in pharmaceuticals, septic tanks, chemistry, mining, oil, electricity plants, municipalities, agriculture, and different fields.
3. Axial Pump
Axial flow pumps include the most well-known types of dynamic pumps. These pumps are used to pump incompressible liquids and to achieve high flow rates with relatively low heads. Therefore, energy transfer from the axial flow pump is only done through the fluid process.
In an axial flow pump, the liquid pump is parallel to the pump shaft. With these pumps, water flows in radially and flows out axially.
4. Hydrant System
A fire hydrant system is a source of water that supplies water at sufficient pressure and flows through the building through a network of fire extinguishing nozzles, pipes, and fire hydrants. This pump has a series of pipes that connect directly to the hydrant in an emergency to supply water to the outlet of the hydrant. Each hydrant pump has several outlet valves to which a fire hose can be connected. This fire hydrant system helps firefighters fight the fire extinguishing process. The fire hydrant system enhances the ability to control fires at the site where firefighters are stationed.
Pros and Cons of Dynamic Pump
Pros
- These pumps are small in size.
- Installation requires a short space.
- The cost is low.
- Maintenance of dynamic pumps is easier than positive displacement pumps.
- You can control low to medium viscosity liquids.
- These are ideal for low to medium head applications.
Cons
- These types of pumps have shaft misalignment issues.
- There is a problem related to impeller damage.
- Wear this pump damage ring for a short time.
- There is a problem with the sealing ring being damaged.
- The bearings of these pumps are quickly damaged by an overshoot.
Application and Uses
- These pumps are commonly used to pump crude oil.
- You work in the chemical industry.
- They are used for commercial and domestic applications.
- These pumps are used in the food industry.
- These pumps are commonly used in the fire protection industry.
- They are used in the production of cellulose, petroleum chemistry, hydrocarbons, paints, and beverages.