Table of Contents
What is Cryogenic Piping?
Cryogenic piping refers to piping networks that operate below -290°C. This temperature represents the embrittlement limit of carbon steel materials, but various references consider piping systems operating below -1500°C (-3000F) to be suitable cryogenic piping systems.
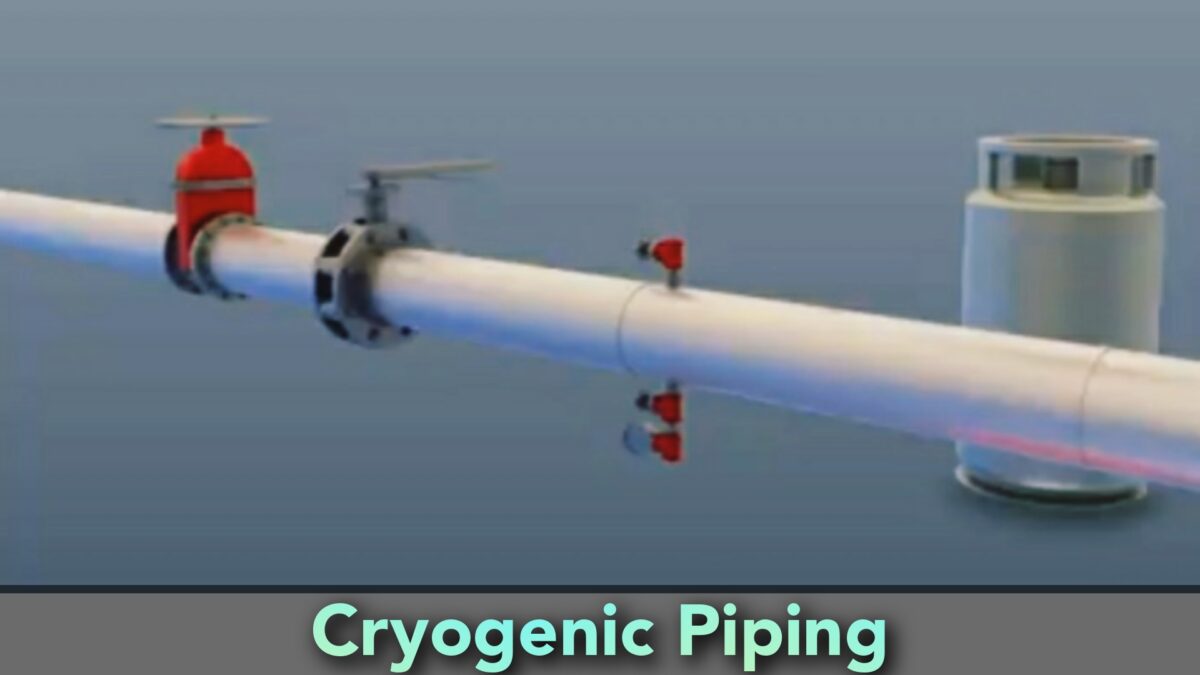
Industrial processing and transportation of propane, butane (LPG), methane (LNG), ethylene, nitrogen, ammonia, and oxygen requires extensive use of cryogenic piping systems. These piping systems must be designed with special care to function at such low temperatures. In this article, we will discuss cryogenic piping in detail.
Characteristics of Common Cryogenic Materials
Cryogenic materials become tasteless, odorless, and colorless when vaporized. Cryogenic liquids can cause skin burns and frostbite and must be handled with care. Table below shows the liquid temperatures and liquid-to-gas expansion ratios for some common cryogenic materials.
Cryogenic Material | Liquid Temperature (0C) | Liquid to gas volume expansion ratio |
Oxygen | -183 | 1: 860 |
Nitrogen | -196 | 1: 696 |
Methane | -162 | 1: 579 |
Helium | -269 | 1: 757 |
Argon | -186 | 1: 847 |
Hydrogen | -253 | 1: 851 |
Fluorine | -187 | 1: 888 |
Why is cryogenic Piping difficult?
Due to the very low temperatures in service, the pipe material is subject to various types of corrosion and wear problems as the chemical and physical properties of the material change. A normal piping system cannot keep the process gas in a liquid state. As can be seen from Table as given above, cryogenic liquids produce large amounts of gas as they evaporate. Therefore, if it evaporates in a closed container, the container may burst under strong pressure. As a result, this cryogenic piping requires special types of materials, fixtures and valves that are different from normal piping systems, making the design of cryogenic piping systems very important and difficult. Some of the requirements for cryogenic piping systems are:
The material shrinks at low temperatures, creating enormous thermal stresses that must be compensated for by adequate flexibility, so it is flexible enough.
All cryogenic lines are insulated to avoid heat absorption from the environment and for safety reasons. All of this adds weight to the tube and makes the cryogenic system stiffer.
Specially designed valves with long stems and extended bonnets are used as cryogenic valves. Using expensive materials increases the cost of your project. Therefore, every optimization opportunity should be taken to minimize the cost of the project.
Cryogenic Piping Materials
As the temperature drops, the material becomes brittle, creating a regulatory impact test requirement. Various parameters should be considered when choosing a cryogenic piping material, such as:
- Adaptability to various manufacturing techniques
- Corrosion resistance
- Oxidation and sulfuration resistance
- strength and ductility
- Suitable for cleaning process
- Toughness, wear resistance, erosion, wear resistance, and sizing.
- Physical properties
- rigidity
- impact resistance, etc.
Materials that have established themselves as suitable cryogenic piping materials are listed in table as given below.
Ferrous Materials | |
Cryogenic Piping Material | Lowest Temperature (0C) for Application |
SA-333 Grade 1 | -46 |
SA-333 Grade 7 | -73 |
SA-333 Grade 3 | -101 |
SA-333 Grade 8 | -196 |
Austenitic Stainless Steel (Grade 304, 304L, 321, 347) | -254 |
Austenitic Stainless Steel (Grade 316, 316L, 316 Ti, 316 Nb) | -196 |
Non-Ferrous Cryogenic Pipe Materials | |
Aluminum Alloy (1100, 3003, 5052, 5083, 6061, 5086) | -254 |
Copper Alloy (C10200/C12200), Copper Nickel Alloy (70600, C71500) | -198 |
Monel 400 | -198 |
Non-metallic materials such as Grafoil, Mineral Wool, Fiberglass, Polyurethane, Styrofoam, Perlite, Viton, and Fiberglass Reinforced Teflon serve as various components for cryogenic piping applications.
Cryogenic Piping Design
ASME B31.3 is the leading authoritative standard for the design of cryogenic piping systems. Typical cryogenic piping design considerations include:
- Pipe sizing is based on normal pressure drop standards. The pressure drop can cause some of the liquid to evaporate, creating a two-phase flow. When similar situations arise, two-phase flow should be considered when dimensioning. However, for oxygen gas lines, flow velocity is also a consideration when sizing the pipe.
- Since the ambient temperature is higher than the temperature of the cryogenic liquid, there is continuous heat leakage from the cryogenic piping and piping system, which must be considered in the design.
- An expansion stem valve is used to keep the actuator at ambient temperature.
Thermal Insulation of Cryogenic Pipelines
All commonly used cryogenic pipes and piping systems are insulated with one of the following types of cryogenic insulation:
- Expanded foam (e.g. foam glass, polyurethane)
- Powder insulation (perlite example)
- vacuum insulation
- vacuum powder and fiber insulation
- milk powder insulation
The primary purpose of cryogenic pipe insulation systems is to create a vapor barrier that prevents atmospheric moisture from entering the insulation space. This moisture penetrates the insulation and condenses. This greatly increases the corrosion variation of the line. Water and ice build-up can also occur, leading to poor performance. Impaired insulation results in loss of thermal efficiency and increased energy consumption. Thus, the use of suitable insulation can reduce high energy consumption. A moisture barrier system must prevent atmospheric moisture from entering the isolation chamber and freezing in the cryogenic line.
Whenever a cooling system is required, the entire system should be completely isolated, including plumbing components, instead pipes/hoses from fixtures, drains, equipment nozzles, and supports. Cryogenic insulation is applied in several layers.
Cryogenic Pipeline Support
Due to the extremely low temperatures, the cryogenic piping support equipment must have excellent heat insulation, durability, and stable operation. Structural properties, design loads, other requirements and economics of each shoe, guide, stop and trunnion should be considered when designing a cryogenic support. The behavior of cryogenic piping, including pipe supports, should be defined, and warm-up and cool-down conditions under normal operation should also be considered. The system experiences the issues such as Thermal expansion and contraction, pipe insulation, material embrittlement, icing around or between supports, large displacements due to rapid phase changes due to large heat fluxes.
Cryo-tube supports must meet the following requirements:
- Weight saving
- High reliability in water and resistance to oil and corrosion
- High weather resistance
- Requires physical strength against compression, bending and shear
- Suitable for mass production
- Low water absorption
- Heat and flame resistance
- It should contain a dense molded layer bonded to stainless steel.
A cold carrier typically consists of:
- high density polyurethane foam
- phenolic foam insulation
- Polyisocyanurate or PIR
Supports must meet design requirements for compressive strength under sustained load, thermal conductivity, coefficient of friction, operating temperature, and flammability. The support span of the cryogenic tube should be much shorter than that of the insulated tube, even considering unexpected thermal deflection of the tube and fluctuations in flow rate, and the support is immediately adjacent to the change in tube orientation need to do it.
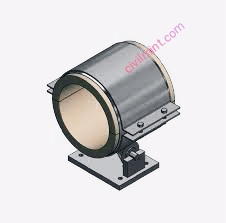
The cryogenic mount is designed with advanced heat resistant technology to protect your tubes in extreme cold. Cold weather is critical for pipe mounts that are not designed to withstand the elements. To make matters worse, pipes are brittle in cold environments, ice buildup can wear out both pipes and supports, and pipes must be designed to support even temperatures as low as -320°F. They encapsulate the fragile insulation used in these piping systems.
The tube must be non-conducting to prevent heat transfer from inside the tube to the surrounding structure. Some shoes are given a foam insulating core to naturally protect the pipes from sudden heat transfer temperature changes.By retaining heat inside the tube, it saves energy and destroys the tube. prevent ice formation that may occur. The Cold Shoe is a support for cryogenic applications that can be used in temperatures down to -300°F, regardless of the heat transferred to the surface.
Stress Analysis of Cryogenic Piping
Cryogenic piping is a special case where the operating temperature used is significantly lower than the installed ambient temperature. Accurate flexibility analysis is critical for managing thermal forces, stresses and displacements due to the required level of rigor associated with operational safety and potential hazards. Considerations for stress analysis of cryogenic pipes are listed below.
- Cryogenic piping systems can have thermal bending effects. Therefore, it should be taken into account.
- For vacuum insulated pipelines, two pipes with different displacements should be considered and connected. At cryogenic temperatures, the main tube contracts and the jacketed tube, which is normally slightly above ambient temperature, expands. Equipment nozzle loads are typically qualified using Finite Element Analysis or FEA.
- Bellows or flexible tubing may be required for analysis.
- Cryogenic pipe systems behave exactly the opposite of hot pipe systems. Contraction of the cold pipeline system causes supports that would normally be lifted in the hot pipeline to bear the load in the cold pipeline.
Closing Thought on Cryogenic Piping
Cryogenic piping refers to systems used in a variety of industrial applications that require cryogenic temperatures, typically below about -300°F (150°C). Because of these low temperatures, cryogenic tubes face unique corrosion and wear problems.Typical examples of cryogenic piping systems include LNG piping and cold box piping.