A gas turbine is a type of internal combustion engine that converts the kinetic energy of gas into rotational (mechanical) energy. This mechanical energy further drives the gas generator, which converts this mechanical energy into electricity.
It is known as a “gas turbine” because it uses gas as the hydraulic fluid.
This turbine can be thought of as an energy converter that can essentially convert the energy stored in the gas into rotational energy. This rotational force drives a generator that produces electricity. After power generation, it is sent to various companies and homes via cables.
Gas turbines are the most common and well-known type of turbine. Gas turbines or gas engines are most commonly used for a variety of purposes around the world. Today, these turbines are the most commonly used power generation technology. These types of turbines are primarily used to generate cheap electricity using gas as the working medium.
Modern gas turbines operate at much higher temperatures than steam turbines. The maximum efficiency of a gas turbine is up to 60%.
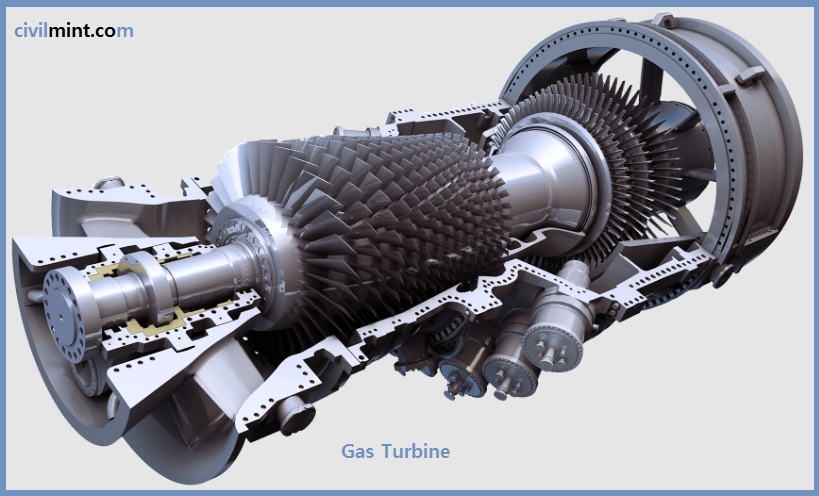
Table of Contents
How does Gas Turbine Work?
Gas turbines operate on the Brayton cycle. During this cycle, the air-fuel mixture is pressurized, burned, passed through a gas turbine, and discharged.
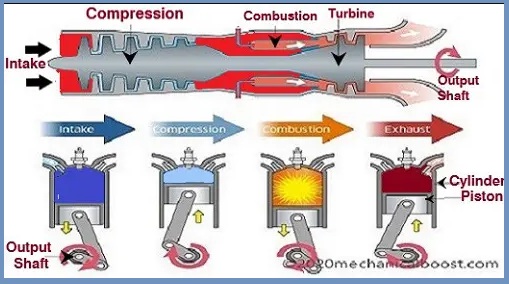
Air is used as the working medium in the gas turbine working cycle. The gas turbine operates in the following stages:
- Suction Process
- Compression Process
- Combustion Process
- Turbine Section
- Electricity Generation
Let’s have a look at these 4 stages of a gas turbine.
1. Suction Process
First, the turbine draws air from the atmosphere into the compression chamber, sends it to the turbine, and sends this air to the compressor.
2. Compression Process
When air enters the compressor, it compresses the air and converts the kinetic energy of the air into pressure energy. It then converts the air into high-pressure air.
3. Combustion Process
After the compression process, the compressed air enters the combustion chamber. The injector injects fuel into the combustion chamber that mixes with the air. After mixing, the combustion chamber ignites the air-fuel mixture. The ignition process turns the air-fuel mixture into a high-pressure, high-temperature gas.
4. Turbine Section
When the combustion gas enters the turbine section, some of the energy in that gas is converted to mechanical energy, and some of the energy is dissipated.
As the combustion gas expands through the turbine, the turbine blades rotate. The rotating blade has two functions. It drives the compressor to draw more air for operation and also drives the gas generator connected to the turbine.
5. Electricity Generation
The generator is connected to the shaft of the turbine. The generator receives mechanical energy from the turbine and converts this energy into electrical energy.
Unnecessary energy escapes from the exhaust. Exhaust gases can be used for external tasks, such as generating direct thrust in a jet turbine engine or driving a second independent turbine (called an electric turbine) that can be connected to a generator, propeller, or fan.
Gas Turbine Working Cycle
Gas turbines operate according to the Brayton cycle. The duty cycle of a gas turbine is explained below using a PV diagram:
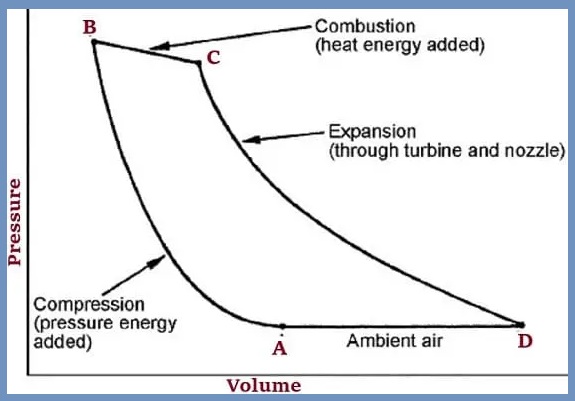
- Compression (A to B): When ambient air enters the compressor, the compressor compresses it and increases its pressure. After compression, air enters the combustion chamber (at point B in the diagram above).
- Combustion (B to C): When compressed air reaches the combustion chamber (path B to C), an injector injects fuel mixed with the air. The igniter ignites this air-fuel mixture, increasing its pressure and temperature at the same time.
- Expansion (C to D): After passing through combustion, air enters the turbine section (lines C to D represent the process), where it expands. As the air expands, it rotates the turbine blades, further rotating the turbine shaft and compressor. Part of the power from this expansion air is used to drive the compressor, while the rest is used to drive the coupled generator. Generators convert this energy into electricity.
Various Types of Gas Turbine Engine
- Turboprop engine
- Jet engine
- Turbofan
- Turboshaft
- Aeroderivative turbine
1. Turboprop engine
The first type of gas engine is a turboprop engine. Turboprop engines include exhaust nozzles, turbines, combustors, compressors, intakes, and reducers.
This gas engine uses a reducer to drive the propellers of an airplane. Turboprop engines are used in small aircraft such as Embraer’s EMB312 Tucano trainer and General Aviation’s Cessna 208 Caravan.
The turboprop engine is also used in large aircraft such as the Airbus A400M Transport. It is also used in medium-sized commuter aircraft such as the Bombardier Dash 8. Exhaust gas drives the power turbine.
The power turbine is coupled via a shaft that further drives the reducer. Turboprop engines require a deceleration gearbox because they achieve the best propeller performance at speeds much slower than the engine’s operating speed.
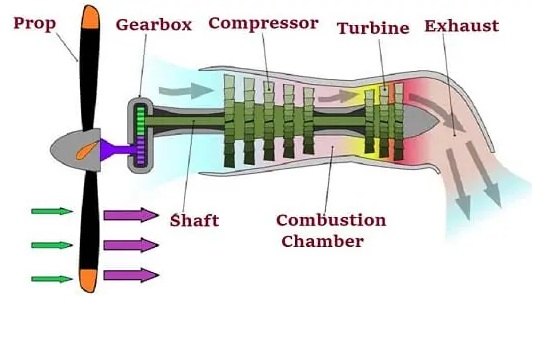
2. Jet engine
The second type of gas turbine is a jet engine. An optimized gas turbine. It uses the exhaust gas or impeller connected to the turbine to generate electricity. An engine that produces power from a direct impulse of exhaust gas is called a turbojet engine. The aircraft uses a turbojet gas engine. First developed in Britain and Germany before World War II, these engines were simpler than other jet engines. The
jet engine has the disadvantages of being noisy and consuming. These engine types have a limited range and durability. These are currently used primarily in military aviation.
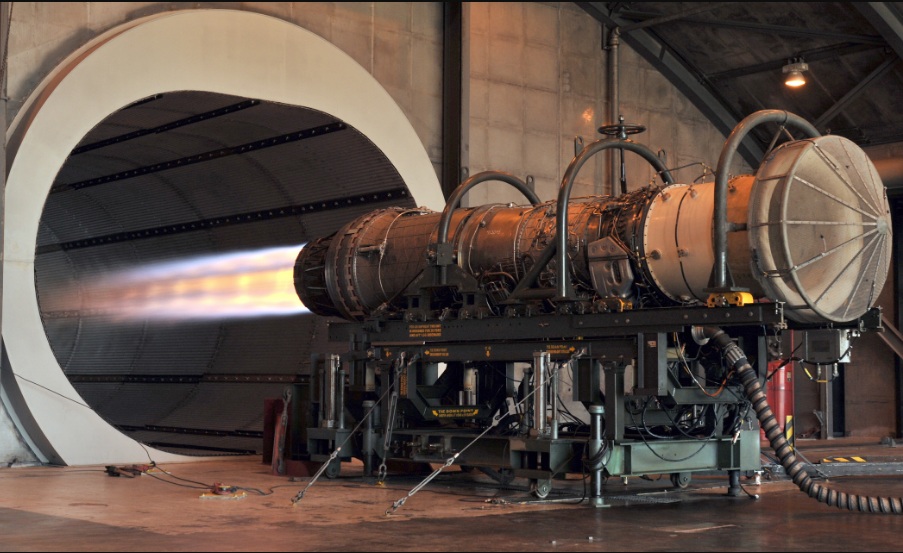
3. Turbofan engine
Jet engines that use ducted fans to generate power are commonly referred to as turbofan engines. The word “turbofan” is a combination of “turbine” and “fan”. The term turbine refers to a gas turbine that draws mechanical power from a combustor, and a fan refers to a ducted fan that draws mechanical power from a turbine to drive it. Sends air backward. This engine uses an impeller and exhaust to generate pulsations. The turbofan engine is also most commonly used on aircraft.
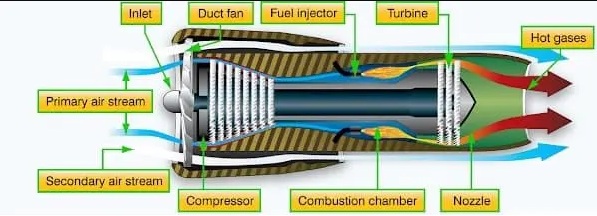
4. Turboshaft engine
A gas engine optimized to generate shaft power instead of jet propulsion is called a turboshaft engine. The operating principle of a
turboshaft engine is very similar to that of a turbojet engine, but with the addition of a turbo, it does an expansion to remove thermal energy from the exhaust and convert it to shaft output. increase.
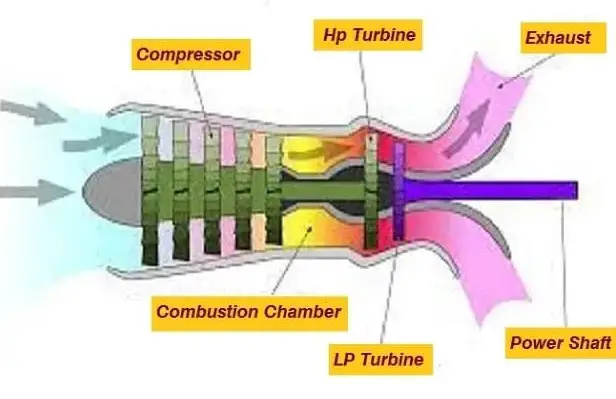
5. Aeroderivative turbine engine
First, they are often incorporated into the gas turbine engines of existing aircraft. Industrial gas turbines are larger than aeronautical diversion turbines. Second, these are used to generate electricity. These turbines are also used in the maritime industry for weight reduction because they stop faster than industrial engines and can react quickly to changing loads.
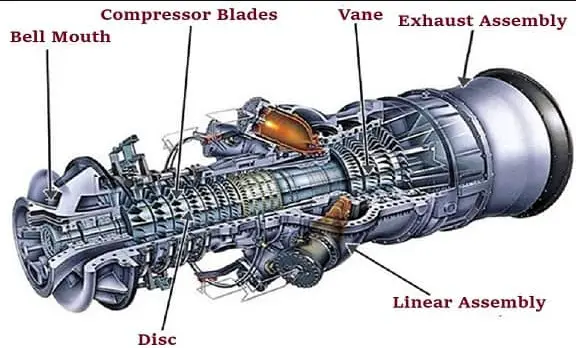
Gas Turbine Performance
The operating temperature (ignition temperature) of a gas turbine affects the efficiency of the gas turbine. The higher the temperature, the higher the turbine efficiency. However, the turbine inlet temperature is determined by the thermal conditions that the turbine blades can withstand.
At maximum, the turbine inlet gas temperature is between 1200 ° C and 1400 ° C. Nonetheless, some designers have raised the inlet temperature to 1600 ° C by developing blade shrouds and cooling systems that protect metallurgical components from thermal damage.
Due to the energy required to operate the compressor, the energy conversion efficiency of a single cycle gas turbine is 20% to 35%, and even the most efficient design is up to 40%.
Exhaust gas retains a lot of heat, which can reach high temperatures of up to 600 ° C as it exits the turbine. Combined Cycle Gas Turbine Power Plants can achieve 55% to 60% efficiency by recovering waste heat and performing more valuable work in a combined cycle configuration.
Components of a Typical Gas Turbine
- Turbine
- Compressor
- Shaft
- Combustion chamber
- Gearbox
- Exhaust
Pros:
- These turbines are easy to transport and ready to start. Global support and service.
- Low cost and low consumption of lubricant. You can use a variety of fuels.
- Due to the excess of air, the air burns completely, the flames on the cold surface do not “extinguish” and the emissions of toxic CO and HC are very low.
- It has high availability.
- Excellent reliability.
- The operating cost is low. Use other clean and renewable fuels.
- Gas turbines have a high output density.
- Releases attenuated gas.
- The construction cost is low. Comprehensive power module block.
Cons:
- High maintenance cost is required. Low power: weight ratio.
- The use of exotic materials can increase the cost of the core engine.
- The efficiency of the gas turbine when idling is lower than the efficiency of the reciprocating engine.
- It has a longer starting time than a reciprocating engine.
- Characteristic complaints can be difficult to manage.
Uses
- These turbines were used to power the plane.
- It is used on the train.
- These turbines are used to propel the ship.
- Gas turbine engines are also used to drive generators.
- These are used to power the pump.
- Gas turbines use gas compressors in a variety of applications.