Table of Contents
What Is Reactive Powder Concrete?
Reactive powder concrete stands out as a special form of concrete that exhibits exceptional strength and ductility. This type of concrete replaced the traditional aggregates often found in ordinary concrete with selected powerful ingredients, including quartz flour, silica fume, and steel fibers. The end result is concrete with an unrivaled range of compressive strengths, from 200 MPa to 800 MPa.
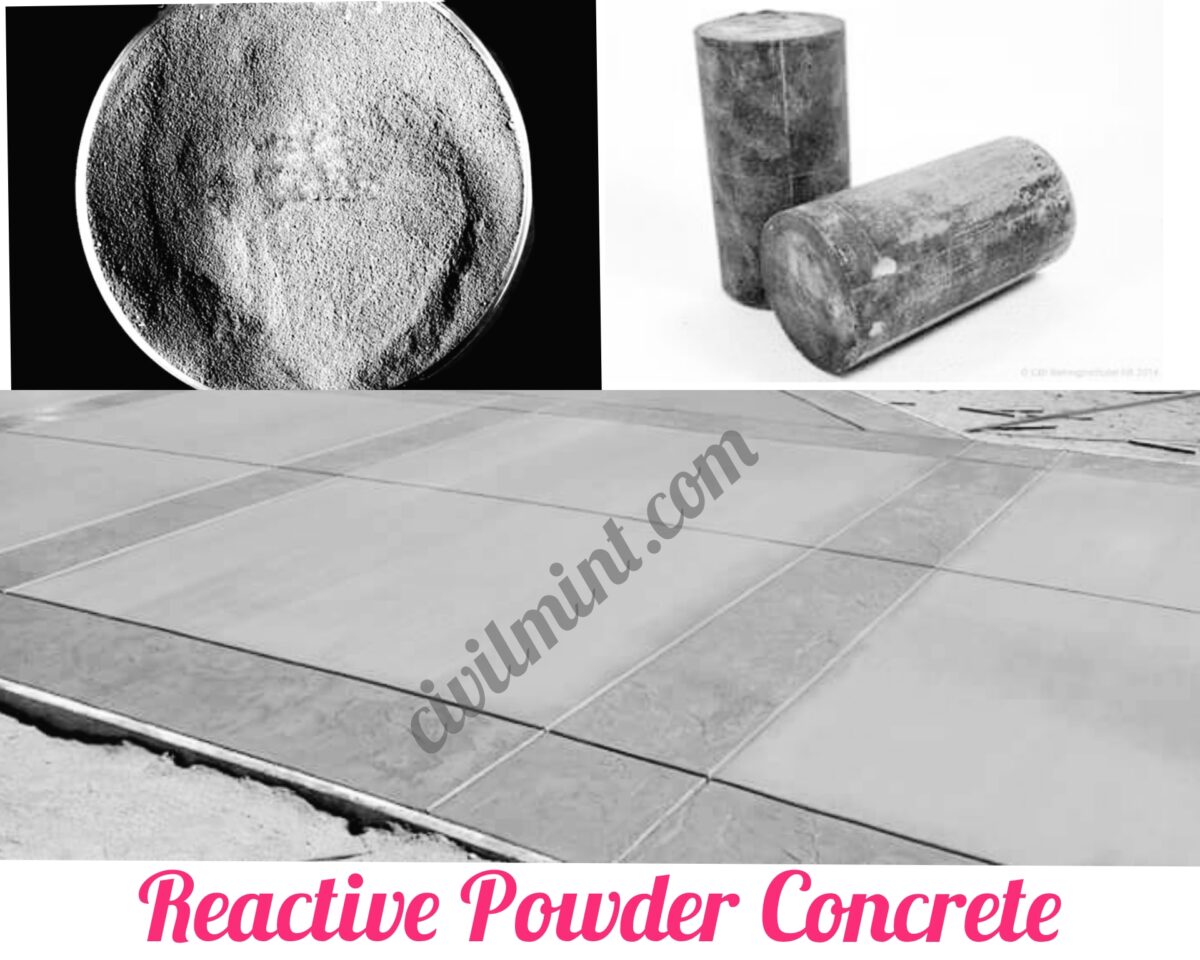
Reactive powder concrete has exceptional strength and the ability to bend without breaking, a property known as ductility. This is very different from the behavior of much more brittle conventional concrete. By adding quartz powder, silicon powder and steel fibers to the mix, reactive powder concrete achieves a harmonious balance between its increased strength and enhanced ability to bend and absorb energy.
I recommend you to read my article on Stress-Strain Curve For Concrete.
The secret to the effectiveness of reactive concrete powder is its precise formulation. Instead of relying on the usual coarse aggregate, reactive powder concrete utilizes the strength of finely ground material. Quartz powder and silica fume combine to form a dense matrix within the concrete, resulting in a structure that is not only extremely strong, but also surprisingly resistant to cracking and deformation.
This revolutionary concrete is ideal for applications where ordinary concrete would shake. It is the material of choice for designing high-performance structures, forming resilient bridges and building critical infrastructure projects. This is especially noteworthy given the wide range of compressive strengths available in crushed reactive concrete, which can be adapted to different project requirements.
It must be recognized that the superior quality of reactive concrete comes at a price. The complex mix design and production process lead to its higher price compared with traditional concrete. However, this investment becomes justified when considering the impressive benefits it offers in terms of strength, flexibility and overall performance.
Properties Of Reactive Powder Concrete
- Strong: Reactive Powder Concrete is very strong, much stronger than regular concrete.
- Easy to Shape: It’s easy to shape and compact on its own.
- Bends Well: It can bend without breaking easily.
- Resists Water: It doesn’t absorb much water and water can’t easily pass through it.
- Stands Cold Weather: It can handle very cold weather without getting damaged
Component Of Reactive Powder Concrete
- Cement: 10-15%
- Fine Quartz Powder and Sand: 70-85%
- Silica Fume: 10-15%
- Steel Fibers: 1-2%
- Superplasticizer: 1-2%
- Water-cement ratio: 0.15-0.20
We will discuss these components in detail.
(a) Cement
Ordinary Portland cement with a medium fineness is suitable for creating Reactive Powder Concrete (RPC). The size of cement particles should range from 1 micron to 100 microns. Cement serves as a binding material and plays a role in generating the primary hydrants of concrete. To make RPC, an optimal percentage of principle minerals or Bogues Compounds are required:
- Tricalcium Silicate (C3S): 60%
- Dicalcium Silicate (C2S): 22%
- Tricalcium Aluminate (C3A): 3.8%
- Tetra-calcium Alumino Ferrite (C4AF): 7.4%
Read also: Difference between ordinary portland cement and pozzolona portland cement.
(b) Sand
For RPC, it’s recommended to use natural river bed sand or crushed sand with a particle size between 150 to 600 microns. The sand should have good hardness and be easily available at a low cost. In RPC, sand particles are the largest in size, contributing to the strength of the concrete mix.
(c) Fine Sand
Fine sand, like river bed sand, is a vital component in RPC.
(d) Quartz Powder
Quartz powder is commonly available in crystalline form and is chosen based on its fineness. The particle size should range from 5 microns to 25 microns. Quartz serves the purpose of providing maximum heat resistance to the concrete.
(e) Silica Fume
Silica fume, derived from ferrosilicon industries, should be selected with low impurity content. The particle size of silica fume is about 0.1 micron to 1 micron. Its functions include filling small voids, enhancing concrete’s flow properties, and aiding in generating secondary hydrates.
(f) Steel Fibers
Steel fibers with a length of 13 to 25 mm and a diameter of 0.15 to 0.2 mm are used to prepare RPC. These fibers improve the ductility of the concrete, making it more flexible.
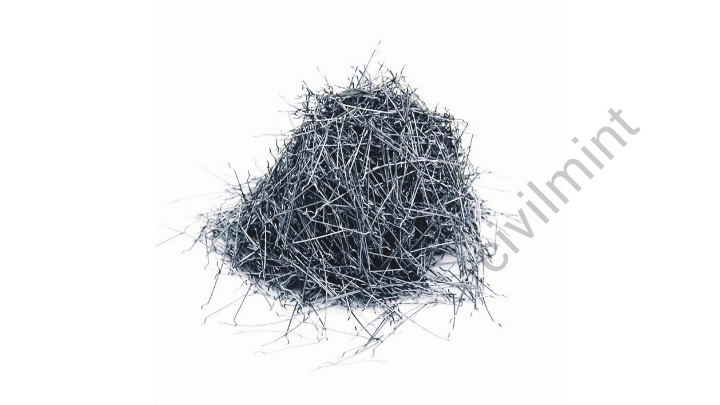
(g) Super Plasticizer
Polyacrylate is employed as a super plasticizer in RPC. Its main role is to reduce the water-cement ratio and enhance the workability of the concrete.
Advantages Of Reactive Powdered Concrete
- Reactive powder concrete is highly flexible.
- This concrete does not allow any gas or liquid to escape, making it very strong and leak-proof.
- It’s like a backpack which is very light but can carry a lot.
- Buildings made of this type of concrete are strong and durable even during earthquakes.
Limitation
Some of the items used to make RPCs are a bit more expensive, making the manufacturing process a bit more expensive.
- Strong: Reactive Powder Concrete is very strong, much stronger than regular concrete.
- Easy to Shape: It’s easy to shape and compact on its own.
- Bends Well: It can bend without breaking easily.
- Resists Water: It doesn’t absorb much water and water can’t easily pass through it.
- Stands Cold Weather: It can handle very cold weather without getting damaged
Applications Of Reactive Powder Concrete
- This is great for making lightweight and long bridges.
- Tall buildings with multiple storeys benefit from its strength.
- RPC works well inside structures that hold water.
- The strength of RPC is very helpful in earthquake prone areas.
- It can be used for anchoring on sea wall.
- Even bridges for vehicles benefit from the properties of RPC.
- RPC can be used in power plant construction.
- It is suitable for railway bridges and light rail stations.
- It is used to make structures that can withstand blasts.
- RPC is used for large concrete works.