A screw compressor is a kind of positive displacement compressor. It utilizes two spiral screws to compress the gases. It works on a positive displacement rotary mechanism for the compression of gas. It has a male rotor and a female rotor for the compression process. The rotors of these compressors have very tight tolerances. The rotor contains many blades that rotate in response to the movement of the rotor. These blades are in close contact and are usually only a few thousandths of an inch apart.
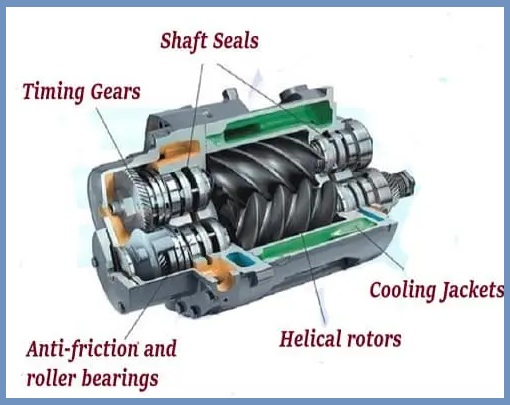
The effectiveness of this mechanism relies upon the precise distance between the rotor and the chamber to seal the compression cavity. However, some leaks are unavoidable, so excessive speeds have to be used to reduce the ratio of leaks to effective flow rates.
Compared to the root blower, the two rotors of the modern-day screw compressors have distinct designs. The male rotor has a convex blade that engages the concave cavity of the female rotor. Male rotors have fewer blades than female rotor blades. Due to the small number of blades, male rotors rotate faster than female rotors.
Screw compressors are the most widely used in various industries around the world. These compressors replace traditional reciprocating compressors that require large amounts of compressed gas. These types of compressors can operate at high shaft speeds with no volume or mechanical losses.
Table of Contents
How Does Screw Compressor Work?
Screw compressors operate on a positive displacement mechanism. It uses two helical rotors to compress air or gas. These rotors mesh so that the concave cavity of the female rotor connects the mesh to the convex blade of the male rotor. The female rotor has more blades than the male rotor. For this reason, the female rotor rotates more slowly than the male rotor. The male rotor is connected to the electric motor via the shaft.
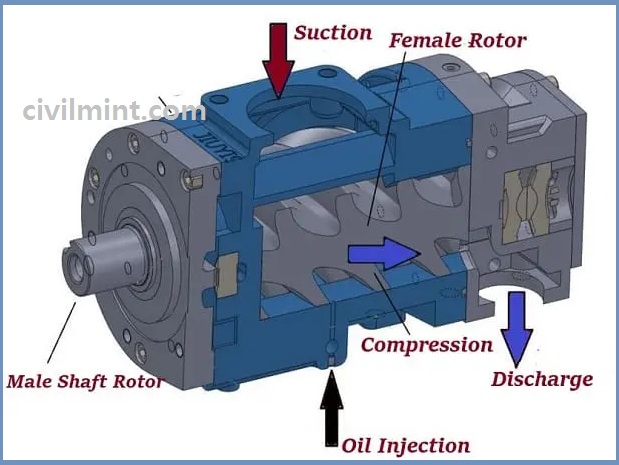
During screw compressor operation, the male rotor is powered by an electric motor through a shaft. When the male rotor is powered by the electric motor, it starts to rotate and also rotates the female rotor.
As these two mesh rotors begin to rotate, a cavity forms at the compressor suction end. Due to this cavity, a pressure difference occurs between the outside and inside of the compressor. Due to this pressure difference, the compressor draws air from the atmosphere into the compressor. This air is trapped between the female and male rotors because the compressor has no way for the air to move directly from the inlet to the outlet.
As the male rotor and rotor continue to rotate, the trapped air also continues to move from inlet to outlet. During this rotation, the blades continuously compress the trapped air. When the air is compressed as needed, it exits the relief valve and is stored in the reservoir.
Parts of Rotary Screw Compressor
- Rotor
- Compression Cylinder
- Air Filters
- Inlet Valve
- Outlet Valve
- Motor
- Housing
You see the below image to understand better.
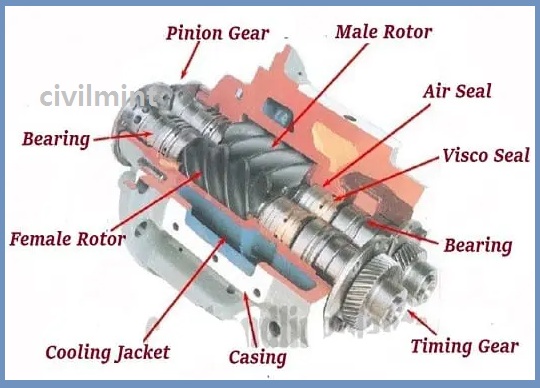
Types of Rotary Screw Compressor
Normally, two types of rotary screw compressors are used. The first is an Oil-lubricated screw compressor and the second is an Oil-free screw compressor.
1. Oil-lubricated screw compressor
These compressors are highly reliable, durable, and efficient. Because of these characteristics, these compressors are best suited for a variety of production processes. Therefore, these compressors are used all over the world for different industries.
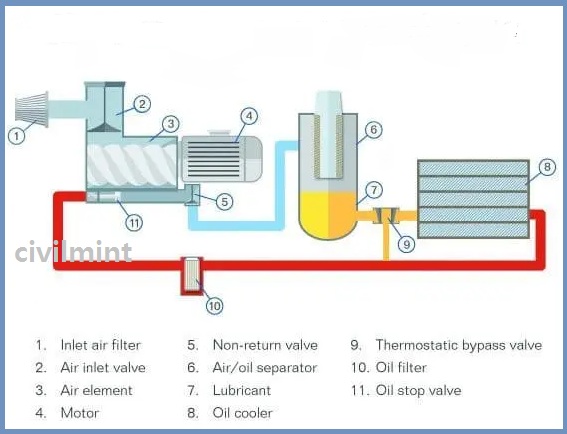
Oil-lubricated rotary compressors are ideal for medium air pressure applications. Therefore, only users of this type of compressor need large volumes of medium-pressure air.
In these compressors, oil is injected into the compression chamber. This injected oil lubricates and lowers the temperature of the compressor components. This oil also helps the compressor to minimize leaks in the compression chamber and remove heat during compression.
Lubricants extend the life of compressor components and also help form a sealing ring. Oil-lubricated screw compressors have low noise compared to others.
Oil-injected screw compressors can run all day without any negative impact. For this reason, this rotary compressor is very advantageous for production applications where compressor downtime can affect production.
Oil-injected screw compressors are also useful for applications where air demand is unpredictable or where you don’t want to control demand.
The compression chamber controls the temperature of the injected oil from 60 to 700°C. The outlet temperature must be kept above the pressure dew point to avoid condensation of water mixed with the oil. The thermostatic valve controls the amount of oil flowing through the oil cooler or bypass to maintain the required temperature over a wide ambient temperature range.
2. Oil-free screw compressor
It is known as an oil-free screw compressor because it uses no oil when compressing air or air. These compressors use lubricants to reduce engine temperature and remove heat through the engine. Some of these compressors use water as an alternative lubricant.
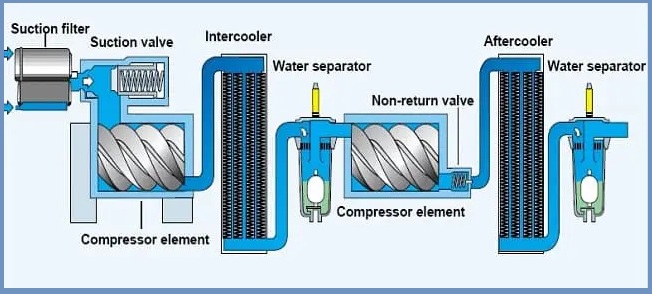
Oil-free screw compressors do not use oil in the compression chamber like oil-based compressors. This compressor effectively eliminates the risk of contamination of the compression chamber without the use of oil.
The oil-free rotary compressor is the best choice when air purity is important to your product and even the smallest impurities can disrupt the process and damage the product. final product. Therefore, many manufacturing industries use screw compressors to make the air pollution-free.
The oil-free compressor is commonly used in sensitive industrial functions. Because these industries adhere to rigorous standards in the pharmaceutical, beverage, and food industries. They are also the best product for the demanding needs of the oil and gas industry.
Benefits of Screw Compressors
- These compressors are running continuously. There is no need to turn the screw compressor on or off.
- Easy to clean.
- There is no duty cycle.
- These compressors are quieter than piston compressors.
- Screw compressors work in the most difficult situations because they have a high airflow rate and work at extreme temperatures.
- These are energy-efficient compressors.
- They require low maintenance costs.
- No capacity is lost over time. These are very efficient for oil flood models.
Some Drawbacks
- These compressors are expensive to install
- Over time, the cost of maintenance or repair of rotating screws will increase
- High service cost
- Experienced operators are required for maintenance
Application and Uses
- These compressors are used to supply compressed air for a variety of industrial applications.
- These compressors are running continuously. Therefore, it is ideal for applications such as automated manufacturing and food packaging systems.
- In the automotive industry, screw compressors are used in ventilation, product finishing, plasma welding, plasma cutting, and air tools.
- These are used in petrochemicals.
- These types of compressors are also used in mining and metallurgy.
- Rotary compressors are used for printing and papermaking applications.
- These are also used in electrical and mechanical machinery.
- They are used for textile and garment applications.
- It is also used for transportation purposes.
- These compressors are also used in construction and building material applications. They use it for home appliances.