Los Angeles Abrasion Test of aggregate is performed to calculate the Los Angeles abrasion value of aggregate and to determine the suitability of aggregates for use in road construction projects.
Los Angeles Abrasion Test is a measurement of the combined strength and resistance to abrasions such as crushing, deterioration, and fracture. This test is suggested by AASHTO T 96 or ASTM C 131. Resistance to breakage of small size coarse aggregates by Abrasion and Impact in Los Angeles Machine.
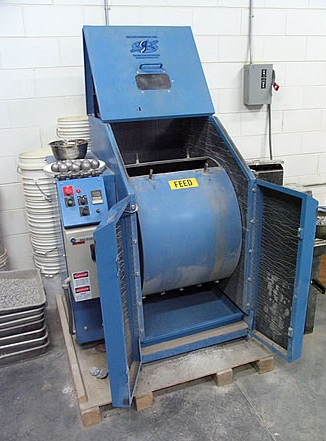
The pavement is made of a variety of aggregates and can be worn by traffic. The movement of a vehicle’s pneumatic tires causes wears on the road surface. Therefore, it is designed to use sufficient hard aggregate in the pavement to resist abrasion.
Therefore, aggregates used in road construction must be resistant to abrasion. The overall abrasion resistance is determined in the test machine’s laboratory in Los Angeles.
The way the Los Angeles friction test works is by using a standard steel ball to provide an abrasive action. These balls mix with the aggregate and also affect the aggregate as it rotates in the drum for a certain amount of time.
There are two methods for calculating the coefficient of wear of coarse aggregates: Los Angeles Abrasion Tester and Devil Abrasion Tester. Many examples show that the Los Angeles Abrasion Testing Machine provides the best overall abrasion resistance results.
Los Angeles Abrasion Test Procedure
Aggregate samples consist of clean aggregate dried in an oven at 105° – 110°C.
The size of the aggregate used in the test is selected to match the grade used for construction as much as possible. Take exactly 5 kg of sample for classes A, B, C, and D and 10 kg for classes E, F, and G. Depending on the aggregate fraction, select the balls of the abrasive mixture according to Table 2. Mount the abrasive rod unit and ball to the cylinder and secure the cover.
After that, spin the machine at a rate of 30 to 33 revolutions per minute. The number of turns must be 500 for classes A, B, C, and D and 1000 for classes E, F, and G. After a set number of revolutions, the machine stops, and the aggregate sample is unloaded into the tray.
All stone dust produced by the machine is sieved through a 1.70mm IS sieve.
Materials larger than 1.7 mm are weighed to the nearest gram.