A diaphragm compressor is a well-known type of compressor from the category of reciprocating compressors. The other name for the diaphragm compressor is membrane compressor. A rotatory compressor is used to compress the air. The rotatory diaphragm enables to supply of the air in the compression chamber and applies the desired strain to supply the air in the desired area.
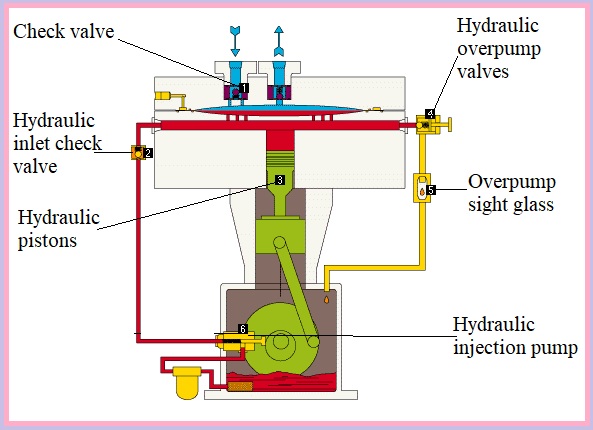
The diaphragm compressor is equipped with a sealed hydraulic piston system to prevent ionic liquids from mixing with the gas. In this compressor, the air is compressed by a flexible diaphragm instead of an air inlet element. The reciprocating diaphragm is driven by a crankshaft and connecting rod mechanism. Diaphragm During compressor operation, the compressor housing, and diaphragm come into contact with hydraulic fluid (gas, air, etc.). Therefore, this compressor is ideal for pumps of explosive and toxic gas.
The diaphragm or diaphragm must be reliable enough to support the stress of the pumped gas. It must also have sufficient heat resistance and chemical properties. diaphragm compression is ideal for situations where the seal needs to be completely separated. Diaphragm compressors are primarily used to treat radioactive, explosive, flammable, toxic, or inert gases.
Table of Contents
Working Concept of Diaphragm Compressor
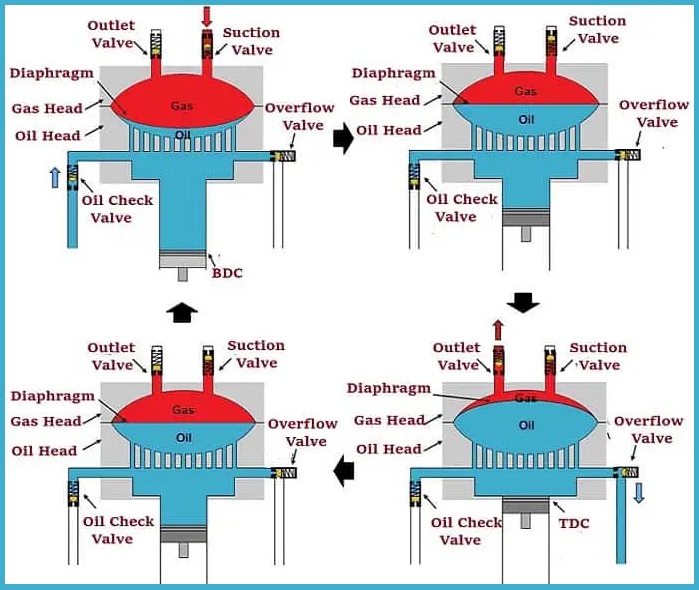
During the operation of the diaphragm compressor, each revolution of the piston supplies a certain amount of hydraulic oil to the diaphragm or diaphragm. This oil helps the diaphragm move up and down. Due to this movement, the membrane compresses air or gas.
When the piston reaches the bottom dead center during the intake stroke, the compensation pump pumps a very small amount of oil from the check valve of the oil head to prevent the piston ring from leaking. As the diaphragm approaches the coil head, the suction gas will not flow through the head. As the piston begins to move towards TDC (top dead center), the internal gas pressure rises above the external gas pressure, which closes the intake valve. After that, the check valve also closes because there is no need to pump hydraulic oil to the compensating pump.
The oil and gas pressure rises quickly until the hydraulic oil brings the diaphragm into contact with the gas head. The pump stroke begins after the membrane comes into contact with the gas head. The coil head is fitted with a pressure relief valve to maintain internal oil pressure. This valve opens and excess oil flows back into the crankcase. When the oil returns to the crankcase, the pump piston begins to move towards the BDC (downstroke), the external gas pressure rises above the internal gas pressure and the exhaust valve closes.
By closing the outlet valve, the gas present in the gas head begins to expand from the outlet pressure to the inlet pressure. When the internal pressure of the gas touches the external gas pressure, the exhaust valve opens and the gas is released. After this process, the entire cycle repeats. Due to the harsh operating environment of the diaphragm or diaphragm compressor, mechanical noise can easily contaminate the AE signal. Generally, the mechanical noise frequency is less than 10kHz.
Parts of a Typical Diaphragm Compressor
- Check Valve
- Overpump Valves
- Piston
- Connecting rod
- Hydraulic Injection Pump
- Crankshaft
Check the below image to know more about parts of the diaphragm compressor.
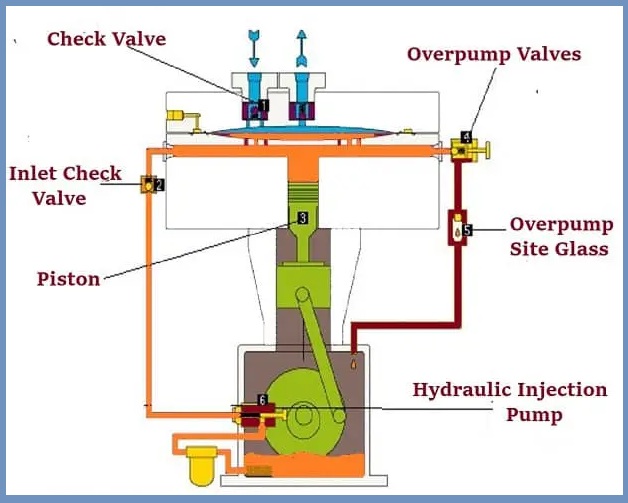
Pros
- Due to the airtightness between the oil chamber and the air chamber, this compressor provides oil-free compression. Its duplex device can compress different gases at the same time
- There is no problem with the transition assembly
- A membrane compressor that is statically sealed to the gas stream ensures wear-free compression. Low stress on crankshaft bearings
- If the membrane fails, it will automatically shut down to prevent damage. Easy to maintain
- Exhaust gas pressure is up to 3000 bar. It ensures a tight compression of the gas. Unmatched high internal pressure saves energy and lowers prices. Silent operation
- This compressor has no vibrations and no knocks
- Save energy
- Extends the life of the membrane
- Reduce energy costs
Cons
- This type of compressor has a low life in the membrane.
- The flow rate is low.
- It cannot be adjusted in itself.
- Valves and piston rings are susceptible to pollution present in the gas.
Some Useful Applications of Diaphragm Compressors
- Diaphragm or membrane compressors are used to clean flat glass.
- Hydrogenation of sesame oil
- Gas mixing, mixing, recycling
- For cleaning some special gases
- Gas for manufacturing glass fiber, semiconductors, and electronic devices
- Syngas compression from renewable raw materials
- Filling gas cylinders and storage tanks
- Metal processing
- Flat glass processing industry
- Also used to cool power plant turbines
- Filling and unloading gas from pipe trailers
- Raw materials for pharmaceutical, chemical, and petrochemical activities
- Hydrogen fuel cell station